东风eq140汽车前刹车调整臂外壳零件的加工工艺及专用夹具的设计毕业论文.docx
《东风eq140汽车前刹车调整臂外壳零件的加工工艺及专用夹具的设计毕业论文.docx》由会员分享,可在线阅读,更多相关《东风eq140汽车前刹车调整臂外壳零件的加工工艺及专用夹具的设计毕业论文.docx(18页珍藏版)》请在冰豆网上搜索。
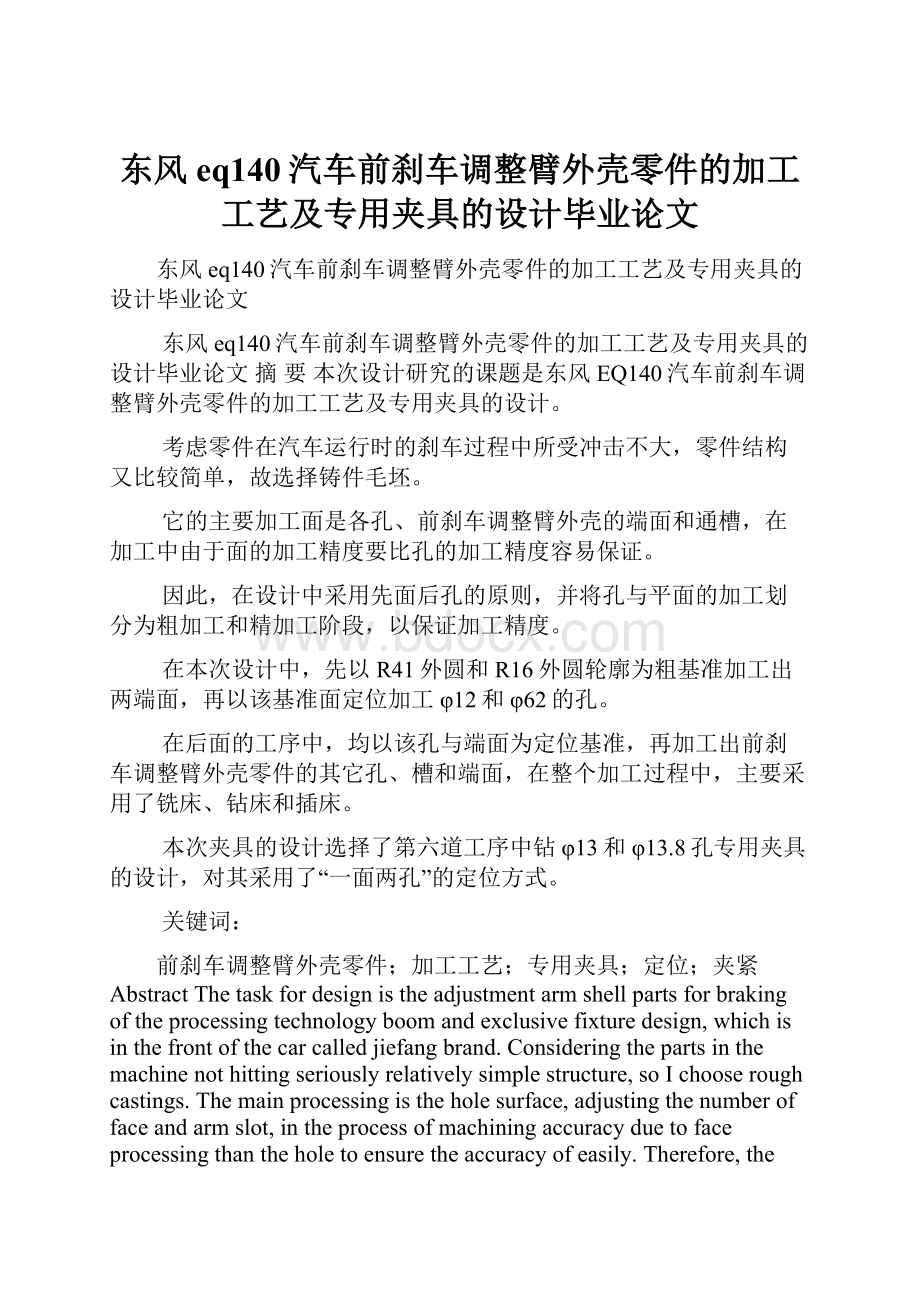
东风eq140汽车前刹车调整臂外壳零件的加工工艺及专用夹具的设计毕业论文
东风eq140汽车前刹车调整臂外壳零件的加工工艺及专用夹具的设计毕业论文
东风eq140汽车前刹车调整臂外壳零件的加工工艺及专用夹具的设计毕业论文摘要本次设计研究的课题是东风EQ140汽车前刹车调整臂外壳零件的加工工艺及专用夹具的设计。
考虑零件在汽车运行时的刹车过程中所受冲击不大,零件结构又比较简单,故选择铸件毛坯。
它的主要加工面是各孔、前刹车调整臂外壳的端面和通槽,在加工中由于面的加工精度要比孔的加工精度容易保证。
因此,在设计中采用先面后孔的原则,并将孔与平面的加工划分为粗加工和精加工阶段,以保证加工精度。
在本次设计中,先以R41外圆和R16外圆轮廓为粗基准加工出两端面,再以该基准面定位加工φ12和φ62的孔。
在后面的工序中,均以该孔与端面为定位基准,再加工出前刹车调整臂外壳零件的其它孔、槽和端面,在整个加工过程中,主要采用了铣床、钻床和插床。
本次夹具的设计选择了第六道工序中钻φ13和φ13.8孔专用夹具的设计,对其采用了“一面两孔”的定位方式。
关键词:
前刹车调整臂外壳零件;加工工艺;专用夹具;定位;夹紧AbstractThetaskfordesignistheadjustmentarmshellpartsforbrakingoftheprocessingtechnologyboomandexclusivefixturedesign,whichisinthefrontofthecarcalledjiefangbrand.Consideringthepartsinthemachinenothittingseriouslyrelativelysimplestructure,soIchooseroughcastings.Themainprocessingistheholesurface,adjustingthenumberoffaceandarmslot,intheprocessofmachiningaccuracyduetofaceprocessingthantheholetoensuretheaccuracyofeasily.Therefore,theuseinthedesignafterthefirstholeoftheprincipleofsurfaceandholeandtwo-dimensionalprocessingisdividedintoroughingandfinishingstagestoensurethemachiningaccuracy.Inthisdesign,thefirstR41andR16atbothendsofthecylindricalsurfaceprocessing,andthenbase-levelprocessingoftheholeofφandφ.Theprocessesbehindbothholeswiththeendofthebaselineforpositioning,processingtoadjustthearmholes,slots,andsomefaceinthewholeprocess,mainlytheuseofthemillingmachine,drillingmachineandslottingmachine.AndforthedesignofdedicatedfixtureIchoosethesixthprocedure,whichdrillstheholesofφandφ,thelocationaredecidedbythe“onesideandtwoholes”.Keywords:
theadjustmentarmshellpartsforbraking;processingtechnology;thededicatedfixture;positioning;clamping目录摘要IAbstractII第一章绪论11.1机械加工工艺的发展现状11.2现代机械加工工艺的发展趋势11.3机床夹具的发展现状31.4现代机床夹具的发展趋势3第二章零件的分析62.1零件的作用62.2零件的工艺分析6第三章零件毛坯的选择73.1确定毛坯的制造形式73.2确定铸件机械加工余量及形状73.3确定铸件加工表面尺寸及偏差8第四章工艺规程的设计94.1基面的选择94.2拟订工艺过程94.3加工设备和工艺装备的选择134.4确定工序尺寸174.5确定切削用量及时间定额20第五章夹具设计325.1夹具设计任务325.2夹具的结构方案确定325.3夹具设计及操作的简要说明39参考文献41结束语致谢附录45第一章绪论1.1机械加工工艺的发展现状随着机械制造业的发展和科学技术的进步,机械制造工艺的内涵和面貌下不断发生变化,近一二十年来的技术进展主要表现在以下几个方面:
1.常规工艺的不断优化常规工艺的方向是实现高效化、精密化、强韧化、轻量化,以形成优质高效低耗、少污染的先进实用工艺为主要目标,同时实现工艺设备、辅助工艺、工艺材料、检测控制系统的成套工艺服务,使优化工艺易于为企业所采用。
2.新型加工方法的不断出现和发展包括精密加工和超精密加工、微细加工、特种加工及高密度能加工、新硬材料加工技术、表面功能性覆盖技术和复合加工,以适应机械产品更新换代对制造工艺提出的更高、更新的制造模式。
3.自动化等高新技术与工艺的紧密结合微电子、计算机和自动化技术与工艺及设备相结合,使传统工艺面貌产生显著、本质的变化,如生产线自动控制、在线检测自适应控制、计算机辅助工艺过程设计、计算机辅助夹具设计、计算机辅助装配工艺设计和智能制造系统等。
1.2现代机械加工工艺的发展趋势机械制造是国民经济各部门科技进步的基础。
在现代条件下机械制造的发展方向是:
开发工艺可行性广、能保证各种原料消耗最少、可靠性和自动化精度高的新一代技术。
机械制造工艺及其实现组织形成的发展趋势,在很大程度上取决于机器结构的发展方向和它的技术使用特征。
机器制造中的科技进步将促进以计算机和生产全盘自动化为基础的工序少和能源节约的工艺的建立和推广。
机器制造工艺组织的远景发展的概念是考虑在集管理、信息和技术为一体的基础上建立全盘自动化工厂,将最终产品的各个加工阶段连接起来。
这时,在科技发展现阶段的自动化工厂将不是无人企业。
由人服务和管理的体系和机器会发挥作用。
新的智能型和集成型的生产手段与高度熟练的工作人员相结合,将在市场需求变化的条件下假造出满足技术和社会经济需求的先决条件。
在先进的发达国家中,毛坯生产的发展趋势表明,今后毛坯生产发展方向是力图在经济合理的范围内,使毛坯接近成品零件的尺寸形状。
这可降低金属消耗量,减少加工余量和毛坯及铁屑的运输费用,这样,最终会提高生产率,降低零件的加工成本。
对于毛坯生产,其特点主要是扩大新的先进的节约资源的工艺过程应用领域。
采用电子技术管理切削加工过程,提高了对毛坯质量和精度的要求。
这将使其加工工艺得到必要的完善。
在不久的将来,精密金属模铸造和压力铸造将取代砂型铸造。
有发展前途的制取毛坯的方法将会得到发展,其中包括等静压法、金属的压力喷射成型挤压、清密冲压、预热推挤方法等。
金属切削加工将被比较经济的制取零件的方法所取代(如冷推挤法)。
但由于所用设备昂贵,以及工件必须经过再次退火,使得这种方法只能在零件生产规模不少于100万件时,经济上才是合算的。
在金属切削机床上加工工艺的发展趋势,是扩大采用先进的工艺过程和提高加工自动化的程度。
提高生产率,降低切削加工成本,在很大程度上取决于刀具和刀具材料的技术可行性。
高速钢和烧结合钨硬质合金,由于价格相对较低,工具制造简单,耐磨性好,强度高,所以促使其得到了广泛的使用。
新型切削材料的使用有助于增大切削用量,提高生产率,扩大经济效益。
使用粉末冶金高速钢工具,并且用物理沉积法涂上耐磨涂层,是很有发展前途的。
对于钢件的半精加工和精加工,采用以碳化钛、碳氮化钛为基的无钨硬质合金。
用细颗粒硬质合金代替高速钢,可提高加工生产率指标。
在加工韧性材料时,涂层硬质合金获得了越来越广泛的应用。
用化学气相沉积方法得到的陶瓷涂层的应用,可使切削速度大大提高,而这种切削速度在以前只有用矿物陶瓷切削刀具或金属陶瓷才能达到。
在加工淬火钢,尤其是铣齿和拉削方面,以及有色金属和合金的加工,非金属材料的加工中,使用硬质合金也是有发展前途的。
在硬质合金刀片上镶上人造材料——多晶立方氮化硼,可用于加工硬度达HRC68的镍铬钢或铬镍钼钢,其切削速度可达130m/min。
在加工研磨性强的,轻金属和非金属材料时,则采用多晶金刚石。
用碳化硅纤维增强的氧化物陶瓷,用于加工镍合金、渗碳和热处理后的钢以及灰铸铁。
氮化硅陶瓷在广泛的切削速度范围下使用(达1000m/min).氮化硅陶瓷现在用于灰铸铁、高温合金的加工,因为它有较高的抗扩散磨损的能力。
陶瓷结合剂的立方氮化硼砂轮、多孔砂轮和数控机床用的砂轮,具有寿命长、磨削性能稳定的特点。
今后在磨削中将使用优质的加入合金成份的刚玉砂轮、用球形刚玉制造的砂轮、高纯度单晶刚砂轮、高强度耐热人造单晶金刚石的复合材料砂轮。
磨料的新型结合剂的开发将扩大高磨削的可能性。
除上述传统切削加工方法以外,还有范围更广的非传统金属加工方法:
电物理和电化学加工方法;微塑性变形尺寸加工法以及将两种以上物理本质各不相同的加工方法合在一起的复合加工方法(化学反应,电腐蚀和磨粒加工等)。
这些非传统方法的合理应用领域,是在那些采用传统切削方法不经济或在技术上不可能实现的那些工序。
这样,切削加工由于具有广泛的工艺可行性,所以它在使用机床的加工方法中仍会占有优先地位。
电加工法,冷、热挤压,粉末冶金都只能在某些特殊领域部分地取代切削加工。
而激光加工具有相当广阔的发展前景,在不久的将来将取代工件外形切割和通孔钻削。
1.3机床夹具的发展现状夹具最早出现在18世纪后期。
随着科学技术的不断进步,夹具已从一种辅助工具发展成为门类齐全的工艺装备。
国际生产研究协会的统计表明,目前中、小批多品种生产的工件品种已占工件种类总数的85%左右。
现代生产要求企业所制造的产品品种经常更新换代,以适应市场的需求与竞争。
然而,一般企业都仍习惯于大量采用传统的专用夹具,一般在具有中等生产能力的工厂里,约拥有数千甚至近万套专用夹具;另一方面,在多品种生产的企业中,每隔3~4年就要更新50%~80%左右专用夹具,而夹具的实际磨损量仅为10%~20%左右。
特别是近年来,数控机床、加工中心、成组技术、柔性制造系统(FMS)等新加工技术的应用,对机床夹具提出了如下新的要求:
(1)能迅速而方便地装备新产品的投产,以缩短生产准备周期,降低生产成本;
(2)能装夹一组具有相似性特征的工件;(3)能适用于精密加工的高精度机床夹具;(4)能适用于各种现代化制造技术的新型机床夹具;(5)采用以液压站为动力源的高效夹紧装置,以进一步减轻劳动强度和提高生产率;(6)提高机床夹具的标准化程度。
1.4现代机床夹具的发展趋势夹具是机械加工不可缺少的部件,在机床技术向高速、高效、精密、复合、能、环保方向发展的带动下,机床夹具也正朝着高精、高效、模块、组合、通用、经济方向发展。
1.高精随着机床加工精度的提高,为了降低定位误差,提高加工精度,对夹具制造精度要求也更高了。
高精度夹具定位孔距精度高达±5,夹具支承面垂直度达0.01/300,平行度高达0.01/500。
德国demmeler(戴美乐)公司制造的长4、宽2的孔系列组合焊接夹具平台,其等高误差为±0.03;精密平口钳的平行度和垂直度在5以内;夹具重复安装的定位精度高达±5;瑞士EROWA柔性夹具重复定位精度高达2~5。
机床夹具的精度已提高到微米级,世界知名的夹具制造公司都是精密机械制造企业。
诚然,为了适应不同行业的需求和经济性,夹具有不同的型号,以及不同档次的精度标准供选择。
2.高效为了提高机床的生产效率,双面、四面和多件装夹的夹具产品越来越多。
为了减少工件的安装时间,各种自动定心夹紧、精密平口钳、杠杆夹紧、凸轮夹紧、动和液压夹紧等,快速夹紧功能部件不断地推陈出新。
新型的电控永磁夹具,夹紧和松开工件只用1~2秒,夹具结构简化,为机床进行多工位、多面和多件加工创造了条件。
为了缩短工件在机床上安装与调整夹具的时间,瑞典3R夹具仅用1分钟,即可完成线切割机床夹具的安装与校正。
采用美国Jergens(杰金斯)公司的球锁装夹系统,1分钟内就能将夹具定位和锁紧在机床工作台上,球锁装夹系统用于柔性生产线上更换夹具,起到缩短停机时间,提高生产效率的作用。
3.模块、组合夹具元件模块化是实现组合化的基础。
利用模块化设计的系列化、标准化夹具元件,快速组装成各种夹具,已成为夹具技术开发的基点。
省工、省时,节材、节能,体现在各种先进夹具系统的创新之中。
模块化设计为夹具的计算机辅助设计与组装打下基础,应用CAD技术,可建立元件库、典型夹具库、标准和用户使用档案库,进行夹具优化设计,为用户三维实体组装夹具。
模拟仿真刀具的切削过程,既能为用户提供正确、合理的夹具与元件配套方案,又能积累使用经验,了解市场需求,不断地改进和完善夹具系统。
组合夹具分会与华中科技大学合作,正在着手创建夹具专业技术网站,为夹具行业提供信息交流、夹具产品咨询与开发的公共平台,争取实现夹具设计与服务的通用化、远程信息化和经营电子商务化。
4.通用、经济夹具的通用性直接影响其经济性。
采用模块、组合式的夹具系统,一次性投资比较大,只有夹具系统的可重组性、可重构性及可扩展性功能强,应用范围广,通用性好,夹具利用率高,收回投资快,才能体现出经济性好。
德国demmeler(戴美乐)公司的孔系列组合焊接夹具,仅用品种、规格很少的配套元件,即能组装成多种多样的焊接夹具。
元件的功能强,使得夹具的通用性好,元件少而精,配套的费用低,经济实用才有推广应用的价值。
大家都知道减少停工检修期是提高生产力、使生产能力利用系数最大化的一项重要因素。
然而零件加工过程中的精确定位和装夹的重复精度也是改进效率和质量的关键。
譬如柔性加工中心的产生就是为了减少产品循环周期。
在一个固定体上,采用机械装夹定位、夹紧工件后,进行切削加工,加工完毕后松开机械装夹定位块,取下已经加工完毕的工件再换新工件上去夹紧,依次往复,这通常是很花时间的一个步骤。
为了实现高产、高效,工件的定位、支撑、夹紧和夹具的快速松开夹紧,以及操作方便、安全都是非常重要的环节。
对于加工一个较大的工件,并且工序间隔时间短,选用半自动化或全自动化的液压夹具是非常具有经济价值的。
液压定位和夹紧是一项非常可靠而且有效的技术。
目前,各种高性能的液压夹具在机械加工中得到越来越广泛的使用。
采用液压夹具具有以下特点:
(1)有效地保证加工精度采用液压夹具安装定位,可以快速准确地确定工件与定位基准之间的相互位置,工件的位置精度由夹具保证,不受工人技术水平的影响,其加工精度高而且稳定。
(2)提高生产率、降低成本用液压夹具装夹工件,无需找正便能使工件迅速地定位和夹紧,显著地减少了辅助工时(装卸工件的时间);用液压夹具装夹工件提高了工件的刚性,因此可加大切削用量;可以使用多件、多工位夹具装夹工件,并采用高效夹紧机构,这些因素均有利于提高劳动生产率与安全性。
另外,采用液压夹具后,产品质量稳定,废品率下降,此时可以安排技术等级较低的工人,有效地降低了生产成本。
(3)扩大机床的工艺范围使用专用液压夹具可以改变原机床的用途和扩大机床的使用范围,实现一机多能。
例如,在立式钻床或摇臂钻床上安装镗模夹具后,就可以对箱体孔系进行镗削加工;通过专用夹具还可将车床改为拉床使用,以充分发挥通用机床的作用,在加工中心有效的行程范围内扩大了加工零件的数量。
(4)减轻工人的劳动强度当采用气动、液压等夹紧装置时,此夹具装夹工件方便、安全、快速,可减轻工人的劳动强度。
第二章零件的分析2.1零件的作用本次设计给定的是EQ140东风EQ140汽车前刹车调整机构中的一个零件——前刹车调整臂外壳,外形结构见零件图(附件1)。
其主要作用是对前刹车调整臂进行支撑和保护,零件主体中心是一个φ的通孔,用于安装带有花键孔的蜗轮。
孔上开了一个宽的矩形槽,用于放置中心带有通孔的蜗杆,其靠插入φ、φ两通孔的蜗杆轴支撑,用键联结,蜗轮蜗杆相互啮合传递扭矩达到调整刹车的作用。
Rc1/8的螺纹孔,装销子连接刹车分泵用。
2.2零件的工艺分析本零件主要用于支撑和保护前刹车调整臂,同时也传递力矩,因此对零件有一定的强度要求。
零件材料选用KT350,最低抗拉强度达到350Mpa,而且可锻铸铁可以承受震动和冲击,成本低,铸造性好。
零件图样的视图、尺寸、公差和技术要求齐全、正确。
根据参考文献[1],零件主要加工表面技术要求分析如下,各加工面字母标识见零件简图(附件2)。
1.以φ孔为中心的加工表面。
这一组的加工表面包括φ孔(T1),φ(T2)二孔以及两孔的上下端面(D1、D2、D3、D4),矩形通槽。
T1的中心孔和矩形通槽起到定位和传递力矩的作用,所以它们的表面加工要求相对较高。
考虑本零件D1、D2、D3、D4表面与其它元件的装配关系,T1、T2两孔的轴线分别与它们的上下端面有一定的垂直度要求。
键槽侧面(D7、D8)分别与φ(T3)、φ(T4)的孔也有一定的垂直度要求,加工时可选择通孔T3、T1孔及端面D2或D4定位。
2.以φ、φ孔为中心的加工表面。
这一组的加工表面包括φ(T3)通孔,φ(T4)通孔,φ沉孔,左右两个端面(D5、D6)和M10(T6)螺纹和Rc1/8(T7)圆锥管螺纹。
T3与T4通孔要保证一定的同轴度,加工时最好在一次装夹下通过钻、扩将两孔加工出。
根据各表面的加工方法所能达到的经济精度及一般机床所能达到的位置精度,该零件要求加工精度低于IT11级,没有很难加工的表面,各表面的技术要求采用常规加工工艺均可以保证。
但在加工中,由于D1、D2面厚度较薄,应考虑增加辅助支撑,减少零件表面加工产生的变形。
第三章零件毛坯的选择3.1确定毛坯的制造形式毛坯的制造形式应根据生产批量的大小,零件的形状和尺寸,零件的受力情况,工厂现有的设备和技术水平及技术经济性等因素来决定。
本次设计加工的“前刹车调整臂外壳”零件,考虑到零件的轮廓尺寸不大,结构复杂程度一般,在工作过程需要承受一定的扭矩,且加工任务为中批量生产,材料为可锻铸铁(KT350),为了使铸件的加工余量小,一模多用(模可重复使用,减少造模时间),提高生产效率,所以选用金属型浇注。
3.2确定铸件机械加工余量及形状根据参考文献[8]表15-5,零件材料KT350,采用金属型浇注时,铸件尺寸公差等级采用CT9级。
根据参考文献[8]表15-7,确定其机械加工余量等级为MA-F级。
再查参考文献[8]表15-8,根据各加工表面基本尺寸,确定其机械加工余量。
铸件的分型面选择及各加工表面铸件机械加工余量见表3.1。
表3.1各表面铸件机械加工余量表面代号基本尺寸()加工余量等级加工余量()说明D1、D340F2.0对称面D2、D4107F3.0对称表面D537F2.5单侧加工D647F2.5单侧加工T166F2.0双侧加工根据参考文献[8]表15-9,成批生产铸件最小通孔直径为,故本零件上直径小于的通孔均不铸出。
为简化零件铸造工艺,缩短铸造周期,同时结合以下因素分析:
(1)加工孔φ时,刀具形成断续切削,影响刀具寿命若,采用铰孔,孔的加工精度难以保证;
(2)对加工φ、φ两孔同轴度有影响;(3)零件侧面(如D1、D2)定位时的可靠性,稳定性。
最终确定矩形通槽亦不铸出。
3.3确定铸件加工表面尺寸及偏差根据铸件表面的机械加工余量,查参考文献[8]表15-6,确定铸件各表面基本尺寸及偏差,见表3.2,毛坯结构尺寸见毛坯图(附件3)。
表3.2各表面铸件基本尺寸及偏差表面代号加工余量零件尺寸铸件基本尺寸铸件偏差铸件尺寸D12.0121616D32.0D23.0323838D43.0D52.53739.539.5D62.54749.549.5T12(单侧)625858第四章工艺规程的设计4.1基面的选择4.1.1选择精基准根据参考文献[1],精基准的选择应尽可能选择所加工表面的设计基准作为精基准,这样可以避免由于基准不重合引起的定位误差。
但当设计基准和工序基准不重合时,应进行尺寸换算。
由零件图(附图1)分析,φ(T1)孔为该零件的主要设计基准,同时结合该零件的结构特点,精加工时多采用“一面两孔”的定位方式,即以D2或者D4面和φ(T1)孔以及φ(T2)孔为基准。
这样的基准统一,定位稳定,夹具的结构设计及操作也较简单。
D1、D2、D3、D4面的半精加工,两面互为基准进行加工,即以D4端面定位,加工D2端面,再以D2端面定位加工D4面,从而不但能保证对称面的尺寸要求,又能保证两面的平行度要求。
对于矩形通槽的精加工,除了用端面(D2或D4)以及φ(T1)孔定位外,为了保证槽的侧面分别与φ(T3)孔和φ(T4)孔的垂直度,宜选用其中一孔作为通槽精加工的定位基准。
4.1.2选择粗基准根据参考文献[1],参照粗基准的选取原则,当零件有不加工表面时,应当以这些不加工表面作为粗基准,这样可以保证不加工表面相对于加工表面具有一定的相对位置关系。
本次设计选择了以φ(T1)孔和φ(T2)二孔的外轮廓为粗基准,选用两个V型块定位,限制三个自由度(、、),加上一个宽支撑板对D2或D4端面起支撑作用(由于D1、D2端面厚度较薄,加工时需增设辅助支撑),限制三个自由度(、、),从而达到完全定位。
选用这个粗基准一方面便于零件的装夹,另一方面又能达到很好的定位要求。
4.2拟订工艺过程4.2.1选择表面加工方法根据各表面加工要求和各种加工方法所能达到的经济精度,查参考文献[8]表15-32~表15-34选择零件主要表面的加工方法与方案见表4.1。
表4.1各表面加工方法与加工经济精度加工表面加工方法及加工经济精度说明D1、D3()粗铣(IT13)—半精铣(IT11)对称面D2、D4()粗铣(IT13)—半精铣(IT11)对称面D5()铣(IT13)D6()铣(IT13)φ孔(T1)粗镗(IT12)—半精镗(IT8)孔较大,不易铰壁厚小,不宜拉φ孔(T2)钻(IT12)—扩(IT11)φ孔(T3)钻(IT12)—扩(IT11