基于超声振动一电镀金刚石线锯切割硬脆材料技术及机理研究.docx
《基于超声振动一电镀金刚石线锯切割硬脆材料技术及机理研究.docx》由会员分享,可在线阅读,更多相关《基于超声振动一电镀金刚石线锯切割硬脆材料技术及机理研究.docx(38页珍藏版)》请在冰豆网上搜索。
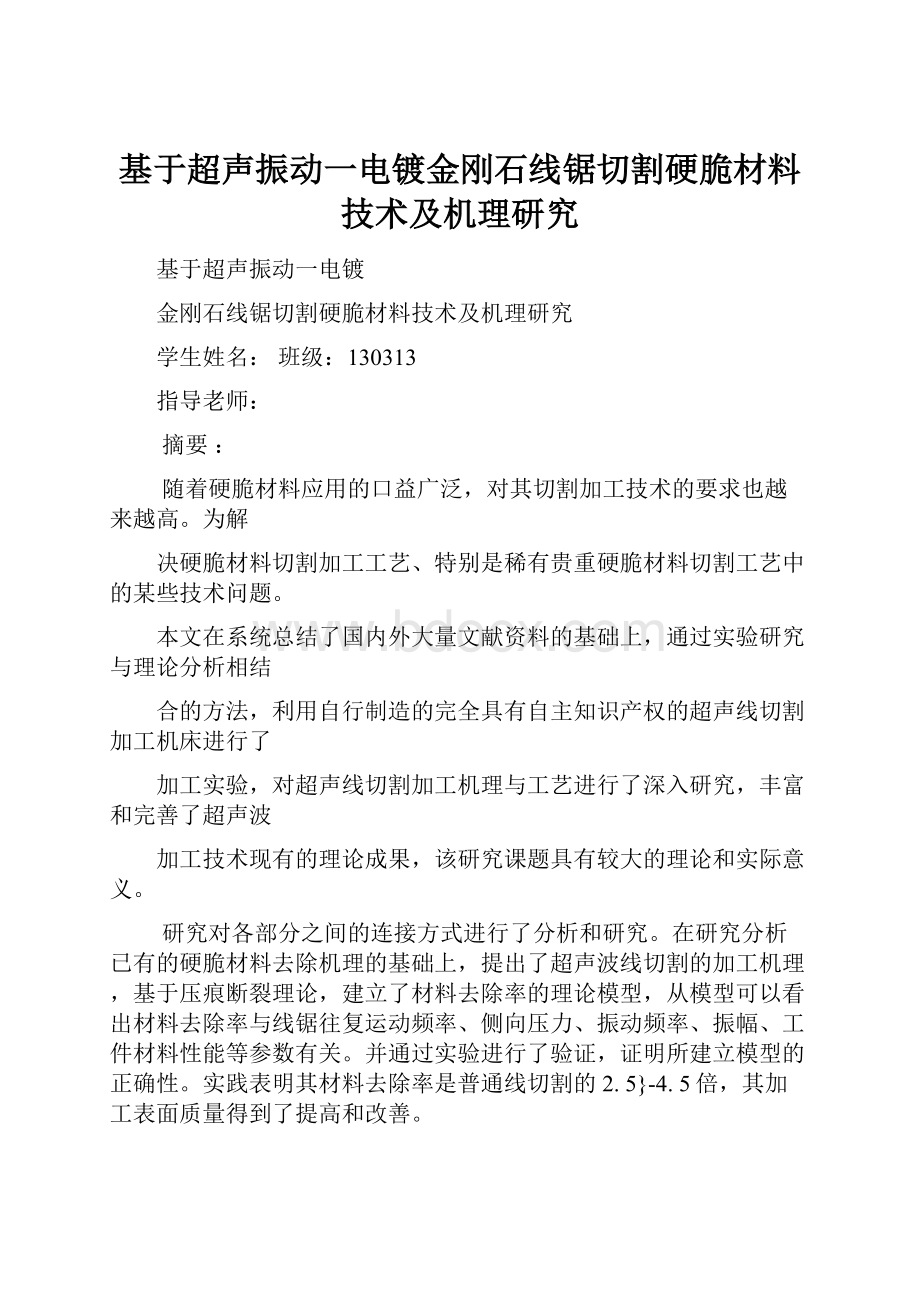
基于超声振动一电镀金刚石线锯切割硬脆材料技术及机理研究
基于超声振动一电镀
金刚石线锯切割硬脆材料技术及机理研究
学生姓名:
班级:
130313
指导老师:
摘要:
随着硬脆材料应用的口益广泛,对其切割加工技术的要求也越来越高。
为解
决硬脆材料切割加工工艺、特别是稀有贵重硬脆材料切割工艺中的某些技术问题。
本文在系统总结了国内外大量文献资料的基础上,通过实验研究与理论分析相结
合的方法,利用自行制造的完全具有自主知识产权的超声线切割加工机床进行了
加工实验,对超声线切割加工机理与工艺进行了深入研究,丰富和完善了超声波
加工技术现有的理论成果,该研究课题具有较大的理论和实际意义。
研究对各部分之间的连接方式进行了分析和研究。
在研究分析已有的硬脆材料去除机理的基础上,提出了超声波线切割的加工机理,基于压痕断裂理论,建立了材料去除率的理论模型,从模型可以看出材料去除率与线锯往复运动频率、侧向压力、振动频率、振幅、工件材料性能等参数有关。
并通过实验进行了验证,证明所建立模型的正确性。
实践表明其材料去除率是普通线切割的2.5}-4.5倍,其加工表面质量得到了提高和改善。
建立了超声波线切割锯切力的理论模型。
该模型以分析单个金刚石颗粒的锯
切力为基础,综合考虑了锯丝速度、工件进给速度、锯丝参数和工件性质对锯切
力的影响。
建立了金刚石颗粒和镍镀层受力情况的有限元模型,分析了锯切时的
应力状态,并由此分析了金刚石颗粒破碎和脱落的原因。
研究认为,锯切过程中,
金刚石颗粒以及金刚石颗粒与镍镀层接触部分的应力都很小,一般不会造成金刚
石颗粒的破碎和脱落,造成破碎和脱落的主要原因是在锯切时的机械冲击作用以
及锯切过程中由于严重摩擦产生的锯切热。
超声波线切割和普通线切割相比其平
均锯切力小、锯切温度要降低,线锯的使用寿命变长。
关键词:
超声加工,金刚石线锯,切割加工,硬脆材料
主要创新点
建立了超声波线切割锯切力的理论模型,以分析单个金刚石颗粒的锯切力为基础,综合考虑了锯丝速度、工件进给速度、锯丝参数和工件性质对锯切力的影响。
该研究课题具有理论和实际意义。
目录
第1章绪论......................................................................................................................1
1.1本课题的研究背景..................................................................................................1
1.2硬脆材料加工方法综述..........................................................................................2
1.2.1圆盘锯切割......................................................................................................2
1.2.2带锯切割..........................................................................................................3
1.2.3线锯切割..........................................................................................................4
1.3超声加工技术国内外的发展概况及发展趋势.....................................................4
1.3.1超声加工技术国内外的发展概况..................................................................4
1.3.2超声加工技术的发展趋势.............................................................................6
1.4本课题的主要研究内容........................................................................................8
第2章超声线切割加工机理及材料去除率理论分析.................................................9
2.1硬脆材料去除机理.................................................................................................9
2.1.1硬脆材料的锯切过程....................................................................................9
2.1.2硬脆材料的压痕断裂力学...........................................................................10
2.2.1超声加工机理...............................................................................................12
2.2.2超声加工材料去除率模型...........................................................................13
2.3超声线切割的加工机理与材料去除率模型........................................................15
2.3.1超声线切割加工机理...................................................................................15
2.3.2超声线切割加工的材料去除率模型...........................................................15
2.4材料去除率的实验研究........................................................................................16
2.4.1线锯的往复运动频率对材料去除率的影响...............................................16
2.5本章小结..........................................................................................................17
第3章锯切力的理论分析及金刚石颗粒与镍镀层受力的有限元分析......................18
3.1金刚石线锯锯切力数学模型的建立....................................................................18
3.1.1锯切力的数学模型.......................................................................................18
3.1.2单个金刚石颗粒所受的锯切力...................................................................18
3.2金刚石颗粒及镍镀层受力状态的有限元分析....................................................19
3.2.1金刚石颗粒及镍镀层受力状态有限元模型的建立...................................19
3.2.2计算参数及载荷施加...................................................................................20
3.3本章小结................................................................................................................22
结论.................................................................................................................................24
参考文献..........................................................................................................................26
致谢.................................................................................................................................28
第1章绪论
1.1本课题的研究背景
随着材料科学的不断发展,各种高性能材料不断出现,它们在工程上具有良好的应用前景。
先进陶瓷材料是现代材料科学发展的重要成果,科学家们曾经预言,20世纪是塑料世纪,而21世纪将是陶瓷世纪。
进入21世纪,已经表明以陶瓷材料为代表的硬脆材料已经同金属材料、复合材料一样正在成为现代工程结构的三大重要支柱之一。
随着我国工业的飞速发展,硬脆材料在各个领域的应用已经口益普遍。
硬脆材料主要包括各种石材、宝石、玻璃、硅晶体、石英晶体、硬质合金、陶瓷、稀土磁性材料等。
硬脆材料大多为非导电体或半导体,通常具有高硬度、高脆性、高耐磨性、高抗蚀性、高抗氧化性、高电阻率、耐高温、不导磁等性能。
由于硬脆材料具有许多金属材料难以比拟的优良特性,因此其应用范围已由建筑业、工艺品制造业等逐渐扩展到航天、机械、汽车、轻工、化工等工业领域(如用玛瑙、宝石等制造轴承,用工程陶瓷制造切削刀具等)。
硬脆材料的推广应用对其加工技术提出了更高要求。
在工业的大批量应用时要求加工成一定的几何形状,有的甚至要求精度很高如作为工C芯片的单晶硅片,加工后要求其表面0.1-0.3,um大小的微缺陷,要求不多于0.05个/cmzcm。
然而,由于硬脆材料具有的低塑性、易脆性破坏、微裂纹以及加工方法选择不当会引起工件表面层组织破坏的缺点。
毫无疑问,使得硬脆材料的加工十分困难。
在硬脆材料的加工中,锯切加工往往是第一道工序,占有很重要的地位。
切割加工的成本约占整个加工成本的50%+.3}。
切割加工是硬脆材料加工的关键工序,其主要工艺要求为:
高效率、低成本、窄切缝(材料利用率高)、无损伤、无环境污染等。
受硬脆材料本身特性的限制,可供选用的切割加工方法比金属切割方法要少,主要是使用各种游离磨料或固结磨料的锯切。
常用的切割方法主要有金刚石锯片切割(包括金刚石框架锯、金刚石带锯等)、激光束切割、高压水射流切割等。
这些切割方法各具优点,也各有其局限性,如金刚石锯片切割一般不能切割曲线,且切缝较宽,出材率较低,不适于对贵重材料进行精密切割。
激光束切割的适用范围较广,但切割深度有限;若采用大功率激光器,则激光与工件间产生的高温等离子体会明显降低加工效率,增加熔融物的排出难度,且设备投资费用昂贵。
高压水射流切割可以切割石材、陶瓷等硬脆性非金属材料,但切缝较宽,不易实现精细的切割加工,且设备昂贵,切割时需耗费大量水资源。
近十几年来,随着硬脆材料在各行各业的应用迅速发展,切割加工硬脆材料的新工艺、新设备不断涌现,其中线锯切割技术发展较快,线切割具有以下优点:
①切割未烧结的硬质合金时,可保证其软边缘不产生破损;②切割脆性晶体切片的
加工效果优于砂轮切割,表面机械损伤层较浅;③金刚石线锯切割加工温度较低,适于切割易炸裂材料;④切割绝缘体不会引起崩碎;⑤可切割精密窄缝;⑥可切割大尺寸切片。
线锯切割加工还具有切片薄、锯口损失小及高效率等优点,因此线切割在硬脆材料的切割方面获得广泛应用。
其中金刚石线锯由于具有独特的结构使其不但能切割各种贵重硬脆材料,而且可以方便地切割曲线。
超声加工(USM)是目前应用比较普遍的一种加工方法,超声加工是利用悬浮磨料对工件的撞击作用和工作液的空化作用去除工件上的多余材料。
超声加工是解决硬脆材料加工难的有效方法之一。
尽管超声加工的生产效率比电火花、电解加工等低,但其精度和表面粗糙度却比它们高,可稳定地加工精度为士Sum,表面粗糙度为Ra<0.51一0.76um的零件[Lj而且超声加工不受工件材料的电、化学特性限制,不需要工件导电。
实践证明,超声加工是加工玻璃、陶瓷、石英、宝石以及半导体材料等硬脆材料非常有效的方法。
1.2硬脆材料加工方法综述
当前,按照切割工具形状分,硬脆材料切割方法主要分为图1.1所示的几类。
图1.1硬脆材料切割方法
1.2.1圆盘锯切割
按照切割形式又可分为外圆锯和内圆锯。
外圆锯以锯片外圆周上的金刚石颗粒作为切割刀刃,是应用较早的切割方法。
金刚石外圆锯自19世纪在欧洲制造「5」,并伴随着人造金刚石的大量生产进入全盛时期。
外圆锯具有效率高、操作方便等优点,但是在切割过程中锯片易偏摆和跑偏,锯片刚性差,噪声大等缺点。
外圆锯切割的线速度较高,在石材加工中可达30m/s,锯切深度受到锯片直径的限制,一般不超过直径的三分之一。
一般情况下锯切深度不超过lm,1997年德国研制出直径达5m的圆盘锯。
外圆锯主要用于石材的切割、房屋、桥梁、路面等建筑的拆除、改建。
为提高生产效率,生产板材多选用先进的多片式圆盘锯,一般不超过30片,多者可达55片「6-8]o
金刚石圆锯片高速旋转时会产生振动和噪声,有时噪声甚至超过110分贝。
噪声不仅会污染环境还会降低切割精度。
口本的Hayasaka等人用计算机仿真的方法研究了锯片的振动模态及频率对噪声产生的影响。
研究表明:
噪声是由锯片的波状振动产生涡流造成的「97。
西班牙的Rios等人用实验的方法研究了锯片空载情况下自然频率和共振频率,结果表明,直径是锯片振动最重要的影响因素,随直径增加,其自然频率下降。
锯片旋转时,自然频率分解成两个非常接近的共振频率,向后和向前传播的波的频率,向后的波的频率和转速成正比,而向前的波的频率和转速成反比。
内圆锯是将锯片周边张紧在一个框架上,利用锯片内孔圆周上的金刚石磨料作切割刀刃进行切割。
当周边张紧时,刀片由圆心向四周产生拉伸变形,增加了刀片的刚性,因此,锯片可以做的很薄,通常可以达到0.2mm。
内圆锯切割技术成熟、稳定性好、切缝窄、材料利用率高等优点,在硬脆材料切割领域中应用广泛。
但是内圆据只能进行直线切割,不能进行曲线切割。
1.2.2带锯切割
带锯是一种使用带状工具加工石材的古老的切割方法,目前主要有框架锯、金刚石带锯和钢片锯。
框架锯的分类方法较多,按其锯框运动轨迹可分为摆式框架锯和平移式框架锯两种类型。
摆式框架锯的锯框作钟摆式运动,在加工过程中存在很大的空行程(占整个行程的3/4),工作效率低。
切割中等硬度花岗石,其平均落锯速度为2cm/h,最高可达3cm/h。
平移式框架锯是针对摆式框架锯的缺点而发展的新式锯机,其主要优点是锯框水平往复运动,不存在空行程,同时采用有排孔的锯条和机械自动化供砂装置,大大提高了工作效率。
在锯切中等硬度花岗石时,其平均落锯速度为3.4cm/h,最高可达5cm/h。
但是,平移式框架锯的锯条不抬起,锯片太薄,钢砂易于挤出,为保持正常切削状态,一般情况下,平移式锯条比摆式的锯条厚度要增加50%左右。
因而降低了出材率,并增加了锯条、钢砂和电力的消耗。
为了克服上述设备的缺点,出现了复摆式框架锯。
其运动轨迹由曲线一直线一曲线组成。
但复摆式框架锯结构复杂,机械磨损大,维修费用高。
为克服这一弊病,国外又研制出巨型下摆式框架锯,其锯框宽度可达3.5m,获得了较理想的锯切效果。
金刚石带锯是以镶焊金刚石烧结块的环形锯条为切割工具。
金刚石带锯于20世纪50年代出现于市场,我国于80年代才开始研制出该类设备,北京有色金属研究总院在不锈钢基带上电镀金刚石颗粒,研制出了电镀金刚石带锯。
带锯条的基带可分为长度1663mm、宽度4.5-lOmm、厚0.4mm和长度2350mm、宽度4.8-lOmm、厚0.48mm等不同型号基带。
和传统带锯不同之处是该锯使用电镀的方法将金刚石颗粒牢固地把持在钢带基体上,锯缝窄,出材率高,并且可以进行曲线加工。
电镀金刚石带锯不仅可以切割石材,还可以切割玻璃等非金属硬脆材料,可进行一定曲率半径的曲线切割,但受到锯条宽度的限制,切割曲率半径不能太小「12]。
1.2.3线锯切割
线锯可分为金刚石串珠锯和金刚石线锯两种。
金刚石串珠锯,是近十几年发展较快的切割工具。
是70年代初期国外开发研制的开采大理石的高效专用设备,首先在意大利矿山推广,应用于石材的开采「13]后来广泛应用于建筑物、桥梁等混凝土结构的拆除和改造,也用于切割玻璃等材料。
金刚石串珠锯由钢丝绳芯、金刚石串珠和隔离套组成,串珠以一定间隔穿在绳芯上,并由隔离套分开。
金刚石串珠锯不但能切割直面,而且还能切割曲面「1A],切割板料时,还可进行多道串珠锯切割,生产效率非常高「川,因此,其用途非常广泛,但受到串珠直径的限制,切缝比较宽,因此,还不能用于细微结构和贵重材料的切割加工。
使用游离磨料的钢丝锯和固结磨料的金刚石线锯统称为线锯。
钢丝锯是利用钢丝快速运动将含磨料的液体带入工件切缝,产生切削作用。
磨液由磨料和矿物油按一定比例混合而成。
常用的磨料为碳化硅。
可以用单根,但常用多根钢丝同时切割。
钢丝锯的主要特点为:
切缝窄,目前最小切缝可达0.2mm,切片量大,切片成本低。
但可靠性差,钢丝耐用度低。
传统的钢丝锯一般为往复式运动,受到钢丝长度的限制,切割速度较低。
固结磨料金刚石线锯通常采用电镀、压嵌和树脂结合等方法将金刚石磨粒镶嵌在钢丝基体上,以此为工具实现切割。
1.3超声加工技术国内外的发展概况及发展趋势
1.3.1超声加工技术国内外的发展概况
超声加工是利用超声振动的工具在有磨料的液体介质中或干磨料中产生磨料的冲击、抛磨、挤压及由此产生的气蚀作用来去除材料,或给工具或工件沿一定方向施加超声频的振动进行振动加工,或利用超声振动使工件相互结合的加工方法。
超声加工系统由超声波发生器、换能器、变幅杆、振动传递系统、工具、工艺装置等构成。
超声波发生器的作用是将220V或380V的交流电转换成超声频电振荡信号;换能器的作用是将超声频电振荡信号转换为超声频机械振动;变幅杆的作用是将换能器的振动振幅放大;超声波的机械振动经变幅杆放大后传给工具,使工具以一定的能量与工件作用,进行加工。
早在1927年美国物理学家伍德(R.W.Wood和卢米斯(A.E.Loomis)最早做了超声加工实验,利用强烈的超声振动对玻璃板进行雕刻和快速钻孔,但当时并没有应用在工业上。
1951年,美国的科恩制成第一台实用的超声波加工机,并引起广泛的关注,为超声加工技术的发展奠定了基础。
从上个世纪50年代以来,许多国家对超声加工技术进行了研究。
口本是较早研究超声加工技术的国家,20世纪50年代末,口本已经设立专门的振动切削研究所,许多大学和研究机构也都设有这个研究课题。
原苏联的超声加工技术研究也比较早,20世纪50年代末60年代初已经发表过很多有价值的论文,在超声车削、钻孔、磨削、光整加工、复合加工等方面均有生产应用,并取得了良好的经济效果。
60年代初期美国就开始了超声加工的研究,70年代中期,美国在超声钻中心孔、光整加工、磨削、拉管和焊接等方面已处于生产应用阶段,超声车削、钻孔、钟孔已处于试验性生产设备原型阶段。
1979年通用超声振动系统已供工业应用。
德国和英国也对超声加工机理和工业应用进行了大量的研究,并发表了许多有价值的论文,在生产中也得到了积极的应用。
例如,英国于1964年提出使用烧结或
电镀金刚石工具旋转超声加工的方法,克服了一般超声加工深孔时加工速度低和
精度差的缺点,取得了较好的效果。
我国的超声加工技术研究始于50年代末,60年代末开始了超声振动车削的研究,1973年上海超声波电子仪器厂研制成功CNM-2型超声研磨机。
1982年上海钢管厂、中国科学院声学研究所以及上海超声波仪器厂研制成功超声波拉管设备,为我国超声加工在金属塑性加工中的应用填补了空白。
1985年以来,超声波旋转加工、超声波布磨装置和变截面细长杆超声车削装置相继研制成功。
20世纪末到本世纪初的十几年间,我国的超声加工技术发展迅速,在超声振动系统、深小孔加工、拉丝模及型腔磨具研磨抛光、超声复合加工领域均有广泛的研究,尤其在金刚石、陶瓷、玛瑙、玉石、淬火钢、花岗岩、大理石、石英、玻璃和烧结永磁体等难加工材料领域解决了许多关键性的问题,取得了良好的效果「川。
经过国内外学者的共同努力,超声加工技术已经取得了显著的进步,研究出加工参数(如超声波振幅、静压力、转速、金刚石类型、磨粒尺寸及连接类型等)与加工结果(如材料去除率、工具磨损等)之间的关系。
建立了有关材料去除的塑性去除、脆性去除等多种去除模型,并进行了实验验证。
1.3.2超声加工技术的发展趋势
超声加工技术已经涉及到许多领域,在各个行业发挥了突出作用,超声加工技术的主要发展趋势有以下几个方面。
1.3.2.1超声振动切削技术
随着传统加工技术和高新技术的不断发展,超声振动切削的研究口趋深入,主要表现在以下几个方面「‘。
(1)研制和采用新的刀具材料
在现代产品中,钦合金、纯钨、镍基高温合金等难加工材料所占的比例越来越大,对机械零件加工质量要求越来越高。
为了更好的发挥刀具的效能,除了选用合适的刀具几何参数外,在振动切削中,人们将更多的注意力转为对刀具材料的开发与使用上,其中天然金刚石、人造金刚石和超细晶粒的硬质合金材料的研究和应用为主要方向。
(2)研制和采用高效的振动切削系统
现有的试验及实用振动切削加工系统在输出功率上尚不够大,因能耗高仍不是很理想。
因此,实用的大功率振动切削系统期待能早口问世。
到目前为止,输出能量为4kw的振动切削系统已经研制出来并投入使用。
在口本,超声振动切削装置通常可输出功率lkw,切削深度为0.01-}-0.06mmo
(3)对振动切削机理深入研究
当前和今后一个时期对振动切削机理的研究将主要集中在以下几个方面:
①在振动切削状态下工件材料是如何与工件分离并形成切屑的。
②振动切削中刀具与工件相互作用的力学分析。
③振动切削机理的微观研究及数学描述。
(4)超声椭圆振动切削的研究与推广
超声椭圆振动切削已受到国际学术界和企业界的重视。
美国、英国、德国和新加坡等国的大学以及国内的北京航空航天大学和上海