曹如意最新开题报告.docx
《曹如意最新开题报告.docx》由会员分享,可在线阅读,更多相关《曹如意最新开题报告.docx(17页珍藏版)》请在冰豆网上搜索。
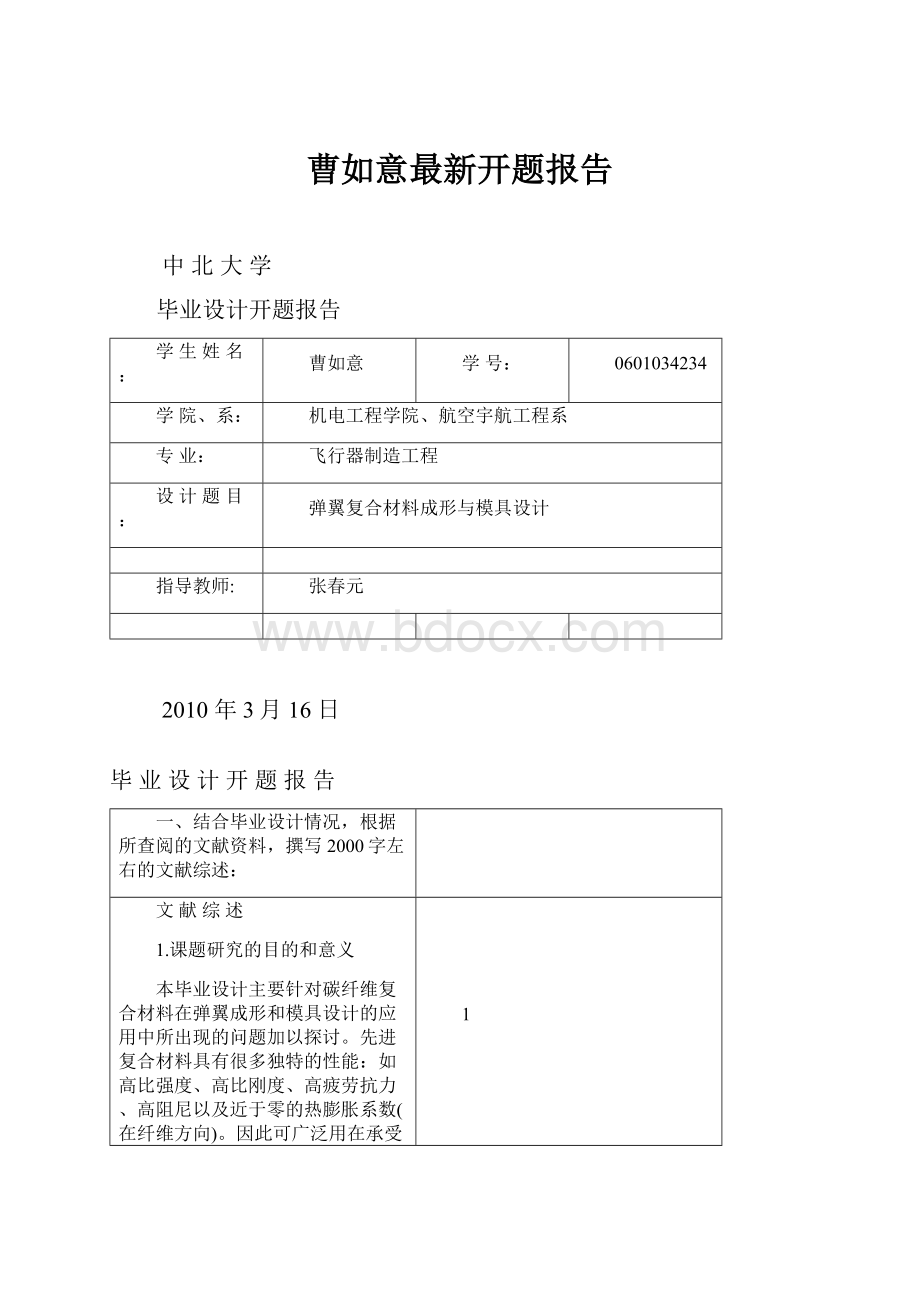
曹如意最新开题报告
中北大学
毕业设计开题报告
学生姓名:
曹如意
学号:
0601034234
学院、系:
机电工程学院、航空宇航工程系
专业:
飞行器制造工程
设计题目:
弹翼复合材料成形与模具设计
指导教师:
张春元
2010年3月16日
毕业设计开题报告
一、结合毕业设计情况,根据所查阅的文献资料,撰写2000字左右的文献综述:
文献综述
1.课题研究的目的和意义
本毕业设计主要针对碳纤维复合材料在弹翼成形和模具设计的应用中所出现的问题加以探讨。
先进复合材料具有很多独特的性能:
如高比强度、高比刚度、高疲劳抗力、高阻尼以及近于零的热膨胀系数(在纤维方向)。
因此可广泛用在承受高温、高温度梯度以厦循环温度变化等严厉热环境下工作的结构中。
1.1纤维增强塑料(FRP)的几种成型方法
目前纤维增强塑料(FRP)作为代替钢铁的结构材料十分引人注目。
FRP的技术研究主要集中在:
①原材料;②成型加工;③复合化以及复合结构设计等几个方面。
特别是FRP的大型产品的成形,以提高生产性和产品性能为目的的成型、加工技术的研究等进展十分迅速。
然而,FRP的成型及加工技术,从手糊成型到各种机械成型范围很广,这里仅以特别引人注目的酚醛树脂、SMC、RTM以及拉挤成型等为内客,简单介绍如下。
1)酚醛型FRP的成型
在FRP的发展历史上,对酚醛FRP的研究从未间断。
然而,以住的酚醛成型工艺是将增强材料浸渍或混合于树脂中,然后干燥,得到子浸料。
此预浸料必须在高温高压下进行缩聚,因而使酚醛的使用范围受到限制。
但是,最近开发了可以在低温、低压下成形的酚醛树脂以及固化剂,与聚醋(UP)一样,能够用于手糊、喷射、注射、模压等各种成型工艺。
另外,PF的特性与UP不同,由于其耐热性、耐燃性优异,在以欧美为中心的国家,应用开发十分活跃。
2)汽车用FRP的新型成型技术
高压注射模内涂层法
SMC材料作为汽车外板应用的重要课题之一,是如何防止因SMC成型制品表面的缺陷引起的涂装气孔的发生。
近年来,采用注射模内涂层法(IMC)和减压脱气成型技术,虽然气孔发生率有所下降,但从汽车大量生产线内式涂装考虑,仍不是十分满意。
最新的技术动向是在成型过程进行处理的高压注射模内涂层法(HighPressureInmoldCoating简称HPIMC)和在成型后进行处理的胺固化底涂法。
HPIMC省略了一介电性底层涂料的涂装工序,IMC与比较,能够成型高膨胀性和高表面质量的SMC,而且对垂直面的涂覆膜厚度可达到以往产品的8倍。
成本低,成型条件控制得当,可以防止气孔的发生。
3)汽车外板用RTM树脂的开发
RTM(Resintransfermolding)成型方法与RI(Resininjection)成型方法类似,适用多品种中等批量产品的生产,可代替手糊成型。
目前的主要产品是以组合式卫生间为中心的建材制品,作为新应用,期望能向汽车以及车辆领域发展。
RTM成型方法的特点是:
①设备费用少;②能够进行带有嵌件的大型产品的整体成型;③适合多品种生产等许多优点,但一般表面加工质量较差,正在进行各种研究以求解决。
4)拉挤成型
有关拉挤成型方法的研究,主要集中于:
①拉挤用树指的开发,如环氧树脂系以及间苯二甲酸系聚醋树脂的研究;②RIM一拉挤成型方法的研究;③拉挤成型时模具内部压力分布的测定等
。
1.2高性能复合材料的低成本制造技术
高性能复合材料的低成本制造技术是目前国际复合材料研究领域中令人瞩目的新发展动向,它打破了长久以来高性能复合材料必然具有高制造成本的惯例,为高性能复合材料开辟了广阔的应用领域。
因此,在已有主要材料体系基础上开发先进的低成本制造技术是当今复合材料界的共识,目前降低复合材料制造成本采用的技术途径主要有:
电子束固化技术、纤维铺放技术、渗透成型技术。
1.2.1电子束固化技术
电子束固化[1~4]即高能量电子束碰撞目标分子,释放足够的能量使其产生一系列活泼的粒子,当邻近分子发生这一过程时,活泼粒子释放出能量,形成化学键。
电子束固化的主要设备是电子加速器。
电子在加速器中被加速,携带高能量与介质分子碰撞,引发介质的交联反应,实现树脂基复合材料的固化。
待固化的材料一般通过传送带或电动小车传送到电子加速器的电子束发射窗口下面接受辐射。
电子束固化过程中的主要参数有:
电子加速器能量、功率、辐射剂量率、辐射剂量、待固化材料的密度、厚度及材料本身的化学性质等。
电子束固化具有节省能源;固化迅速;工装简易;工艺灵活性大;工艺匹配性好;无挥发物释放等优点。
1.2.2纤维铺放技术
复合材料纤维铺放成型技术是自动铺放丝束成型技术和自动窄带铺放成型技术的统称,是在已有缠绕和自动铺放基础上发展起来的一种全自动制造技术。
纤维铺放成型设备由旋转芯模和多自由度的铺放头系统构成,它由计算机协调系统控制成型过程。
按照结构所确定的铺层方向和铺层厚度,用多自由度的铺放头将多组纤维预浸纱束/窄带自动铺放在旋转的芯模表面,铺放过程中同时加热软化预浸纱束/带,压实形成制品型面。
纤维铺放技术兼备了纤维缠绕和自动铺带的优点,但比纤维缠绕和自动铺带更先进,对制品的适应性更强。
纤维缠绕技术具有高效、自动化和低成本的优点,但必须满足:
落纱稳定;纤维连续缠绕;正缠绕张力3个条件。
其中落纱稳定确定了纤维轨迹必须按曲面测地线或准测地线,从而限制了纤维方向的设计自由度;纤维连续缠绕要求纤维分布必须满足周期性条件,限制了成型厚度及分布的自由度;正缠绕张力决定了纤维缠绕只能在Gauss曲面上进行,难以完成凹面缠绕且成型压力随曲面曲率和纤维轨迹变化。
自动铺带技术高效、高质量,但由于采用宽带(75~300mm)和单自由度铺放头,不能完成复杂曲面、变厚度、加强筋等成型。
纤维铺放技术解决了上述问题,由于采用预浸料和低张力,因此不受落纱稳定性的约束,可以根据设计要求选择铺层方向;由于每根丝束具有单独增加和切断功能,因此不受周期性约束,可以实现形体和各种铺层设计;由于采用压辊成型,既可以实现任意曲面的成型又可以保证成型压力自动可控,提高制品质量;由于采用多丝束的铺放头一次铺放较宽的丝带,因此大大提高了生产效率,而且具有表面光洁、精度高、速度快、质量稳定性能好的优点,特别适合于航空、航天复合材料结构小、批量化、高精度的要求,实现柔性制造。
对于热固性复合材料体系,成型后既可以采用传统方法放入热压罐固化,也可以与电子束固化技术相结合,边铺放边固化从而取消热压罐;对于热塑性复合材料体系,一般在铺放过程中直接加热固结成型,这对低成本制造技术具有极大的吸引力。
1.2.3渗透成型技术
渗透成型技术包括:
RTM、真空树脂传递模塑(VRTM)、结构反应注射成型(SRTM)、RFI和SCRIMP等。
它们的共同特点是:
1)一般情况下可不采用热压罐;
2)仅真空压或低外压;
3)要求树脂有低的粘度;
4)制造周期短;
5)不用预浸料;
6)劳动工时少;
7)辅助材料消耗少;
RTM、VRTM和SRTM适于复杂型面三维结构的整体成型,因而模具数量、铺层工时、零件数目和机械装配量都可大幅度节省,成本显著下降。
如Cy2com5250-4RTM树脂已成功地用于F-22飞机的复杂型面梁的制造,它比用预浸料铺叠制备梁的方法节省成本20%,隐身飞机F117A发动机的进气道格栅也是采用RTM制造的。
RFI是一种树脂沿结构件厚度方向由下至上的渗透方法,它的渗透距离较近,因而可采用常温下为高粘度(如2~10Pa.s)的树脂体系。
RFI适于制作大型复杂型面、带加强筋条的构件,为确保结构的型面公差与结构完整性,首先要制作出符合要求的纤维预成形体。
预成形体可以是3D、2.5D编织物,也可以是精编、精纺织物。
RFI工艺的关键技术:
一是预成形体的设计及铺设;二是模具设计和全过程中的尺寸控制。
目前最受关注的预成形体成型制作技术是铺叠加缝纫技术,它的要点是将纤维制品按预定方向铺放预成形,用纤维将它们缝纫成为一个整体,从而提高了复合材料件抗冲击的能力,显著减少了零件数量,减轻了结构重量,降低了结构成本。
SCRIMP仅需单面模,另一面为真空袋,借助真空吸力,利用特殊网布作为介质,将树脂吸入预先铺好的纤维编织物中。
SCRIMP既可用于板件的制造,又可用于蜂窝夹层结构的制造,还可以在结构内表面镶嵌加强筋、内插件、连接件以满足不同用途的需要,它对单曲面、双曲面乃至复杂型面的结构都有良好的适应性。
它的模具简单,对模具材料要求不太严格,特别适合于大型结构件的生产
。
1.3开展碳纤维复合材料在弹翼上的应用的意义
碳纤维复合材料弹翼的应用越来越受到重视和青睐,应用范围也逐步扩大。
在主承力结构件上采用复合材料制造越来越多,开展某型碳纤维复合材料弹翼应用研究是市场的发展要求,其意义为:
(1)减轻飞行器的重量,增大射程和有效载荷,提高飞行器系统的机动性能;
(2)为减少工时、降低生产成本,缩短弹翼制造周期提供了可能。
在短时间内完成某型碳纤维复合材料弹翼结构设计;成形模具没计和制造;还有工装夹具的设计和制造;碳纤维复合材料弹翼的成形工艺研究,包括翼型面和主要尺寸检测、静强度试验等。
研制的复合材料弹翼外形尺寸、接头尺寸、孔径、孔边距尺寸公差等技术指标,均达到设计要求
。
2.国内外研究的状况
2.1复合材料整体成形技术在国外已研发多年,并已获得广泛应用,现择要例举如下:
(1)日本的F-2战斗机。
日本于上世纪90年代研制的F-2战机,共用18%的复合材料,包括机翼、垂尾、平尾等,其中机翼下壁板大量采用了以共固化技术为核心的整体成形技术,为此专门制定并执行了ASIP(AircraftStructureIntegrityProgram)计划,见下图。
从图中可见,在机翼下壁板有大量共固化的梁与肋,亦可想见其模具和成形技
术的先进和复杂。
执行ASIP计划的结果实现了减重250kg,引起了美国的关注,美国甚至向日本学习该项技术。
(2)B-2隐身轰炸机:
B-2有两块大的外翼蒙皮,尺寸大到19.8mm×3.66m,规模可观,为复合材料加筋板结构,其上有共固化前后梁和多个翼肋,采用了整体成形技术制造。
(3)F/A-22“猛禽”战斗机:
其机翼主要由复合材料制成,两个机翼共有4大块整体成形的蒙皮壁板,每块尺寸为5.49mm×5.18m,重量为113kg,蒙皮制造中采用了自动铺带(ATL)技术。
(4)F-35战斗机。
在JSF原型机阶段,在美国CAI计划的指导下,波音飞机公司制造X-32飞机,洛马飞机公司制造X-35飞机,这两家公司均选用了进气道为验证对象。
如波音的复合材料进气道,材料为IM-7/977-3,采用了先进的自动纤维铺放(AFP)技术制造,由原来的3大块简化为一大块,重量由91kg减少到59kg,总成本有较大的下降。
(5)JSF无紧固件水平尾翼的制造。
美国波音飞机公司研制出无紧固件的水平尾翼,应该说这是整体成形技术的一个创新。
该水平尾翼的展长为1.37m,根弦长为2.90m,尖弦长为0.61m,沿展向有8个盒形加强件,在共固化中采用铝制芯轴,靠精确计算的热胀压力将加强件压在两侧蒙皮上,固化完毕冷却后将铝芯轴抽出,形成了平尾的主受力盒。
实质上这是一种硬模成形技术。
欧洲空客集团的A330和A340垂直安定面零件数由2000个减少到20个;美国雷神飞机公司首相I(PrimerI)公务机的机身采用整体成形技术、AFP方法生产的零件数由16000个减少到6000个;美国V-22倾转旋翼机的RO-TORGRIP系统零件数由221个减少到5个;美国扩展复合材料应用的“超大黄蜂”F/A-18E/F零件数减少了42%,减重158kg。
复合材料整体成形技术效益的主要量化指标有3个:
零件数的减少、紧固件数的减少、重量的下降,最后又归结为一个要点,即成本的降低。
这就是国外均在低成本计划项下大力发展该技术的原因。
低成本复合材料技术乃是当今复合材料技术发展的核心内容之一
。
2.2国内在“碳纤维复合材料在弹翼上应用”的进展
国内在该课题的研究上以北京机电研究所的张兴益教授为首,已经取得了成功并应用与实践。
经过多年的研究,他们解决了大尺寸复杂构件的模具设计制造和带有主接头的骨架整体铺层、固化、组装等工艺关键,研制成功符合要求的碳纤维复合材料弹翼。
该弹翼蒙皮和骨架全部用碳纤维制造,基体材料用628#环氧树脂,整体结构质量比铝合金壁板弹翼减轻40%以上。
碳纤维复合材料弹翼外形见图一。
碳纤维复合材料弹翼具有以下特点:
1)质量减轻明显。
与铝合金壁板结构弹翼相比,该弹翼质量减轻45%,从而达到了设计要求。
2)承载较好。
首次采取弹翼主接头和各桁条、边框条、整体成型工艺,确保弹翼的承载能力。
最终已达设计载荷的150%,而且主接头完整。
3)材料来源丰富。
该弹翼从研制到批试生产,都采用国产材料,不受国际环境的影响。
4)效益显著。
铝合金壁板结构弹翼机械加工工序复杂,加工难度大,既费工又费料,原材料利用率只有8%而复合材料原材料利用率可达98%,碳纤维材料可以充分地被利用,成型工艺较简单,工时明显减少,仅是机加工时的1/4,从而达到降低成本之目的
。
参考文献:
[1](英)C.D.拉德、(美)K.N.肯德尔、C.G.E迈根,复合材料液体模塑成型技术,王继光辉,李新华译,化学工业出版社
[2]黄家康,岳红军,董永祺,复合材料成型技术,化学工业出版社
[3]杨俊华,化工部成都有机硅应用研究中心
[4]好远开,肖加余,高性能复合材料学,化学工业出版社
[5]王善元,张汝光,纤维增强复合材料,东华大学出版社
[6]刘向阳,复合材料模具设计制作技术探讨,硕士学位论文,西安:
西工大,2006
[7]张兴益,高志强,刘华,碳纤维复合材料弹翼研制与质量控制,北京:
306所
[8]欧国荣,倪礼忠,复合材料工业与设备,化学工业出版社
[9]艾涛,王汝敏,低成本、高性能复合材料的成型技术,西北工业大学应用化学系
[10]陈绍杰,浅谈复合材料整体成形技术沈阳飞机设计研究所
[11]NickDavinicandBillBrauni,NavalResearchLaboratory,Washington,DC20375-5320;WayneSimon,AlliedSignalTechnicalServices,Columbia,MD21045,Columbia,MD21045,UseOfAdvancedCompositeMaterialsinSpacecraftStructuralDesign
[12]朱耘玑,邱海鹏,孙明等,C/C-SiC复合材料两种制备工艺及材料性能,北京航空制造工程研究所
[13]PrewoKM.Fiber-reinforcedceramics:
newopportunitiesforcompositematerials.AmCeramSocBull,1989,68
(2):
395-400.
[15]齐乐华,工程材料及成形工艺基础,西北工业大学出版社
[16]张兴益,杨鸿昌,碳/环氧复合材料弹翼的质量控制,北京机电技术研究所
[17]吴人洁,复合材料,天津大学出版社,国家九五重点图书
[18]王汝敏,郑水蓉,郑亚萍,聚合物基复合材料及工艺,科学出版社
[19]内田盛也编著,石行,朱立群等译,航空工业出版社
[20]鲁云,朱世杰,马鸣图等编,先进复合材料,机械工业出版社
1
毕业设计开题报告
二、本课题要研究或解决的问题和拟采用的研究途径:
1.弹翼成形与模具设计
碳/环氧复合材料弹翼的研制主要为解决弹翼的模具设计与制造、弹翼成型的工艺方法,目前还有许多技术问题尚未解决。
如弹翼主接头的尺寸配合公差,包括弹翼接头连接孔的公差;各道工序的定位基准问题;弹翼水平测量点、弹翼的胶接质量等问题尚未彻底解决。
1.1弹翼结构特点
(1)带有前后接头的框架与较薄的外蒙皮铺层为一体,采取模压共固化成半翼,结构零件少;双曲面的外型面,以及合理的结构布局,因此弹翼具有重量较轻、承载强度较高的特点。
(2)接头处预埋钛合金螺套,弹翼扩孔不损伤纤维,可充分发挥碳纤维增强作用,也体现复合材料结构件应用的优越性。
1.2结构对模具的要求
根据弹翼结构设计要求,蒙皮与骨架必须一体成形。
孔边距、半翼蒙皮厚度公差要求很严。
模具采用阴阳模,使用设备是热压机。
在阴模上有的构件质量要求较高,配合零件较多。
例如芯块的型面与阴模型面要吻合一致,而且芯块厚度公差关系到蒙皮的厚度,所以公差要求较高;另外在其根部零件边条的平面度、直度加工精度要求也较高,因为它与阴模的配合间隙关系到孔边距的尺寸公差,也关系到产品的定位基准。
弹翼组装模必须是对称型面的,阴模左右件,确保弹翼的型面符合理论型面要求。
另外配有主副接头的定位块,控制接头槽口尺寸公差符合结构设计公差要求。
因为主副接头尺寸是协调尺寸,对接后的松紧要合适,连接螺栓顺畅插人。
1.3成形模具构成
(1)半翼成形模具构成
主要由阴模与阳模两大件组成。
左半翼产品使用的是左阴阳模具一套;右半翼产品使用的是右阴阳模具一套。
阴模零件较多,带有翼型面的芯块,挡边条。
定位导向柱,定位支架桥,每个支架桥有定位孔和固定螺钉等。
(2)弹翼组合模具构成
带有对称型面的阴阳模、导向柱,在模具周边均设置紧固螺栓等,另外,主副接头分别设计制造标准定位块,控制复合材料弹翼槽口尺寸公差符合要求。
1.4模具设计原则和要求
(1)首先考虑是用什么设备和工艺条件成形,模具的结构形式。
如:
半翼成形模具阴模见图1
(2)尺寸公差应满足结构弹翼尺寸公差,计算并考虑钢模与材料的热膨胀量。
在原结构弹翼设计尺寸公差的基础上提高公差精度。
(3)设计成形模具应确定阴阳模具的分离面,还留有流胶槽和溢料空间。
(4)确保各零件准确定位,应有定位机构和固牢方式。
(5)应选用标准件和通用件,方便使用。
1.5模具设计
运用Solidworks三维绘图软件绘制模具图和用AutoCAD绘制工程图
1.6弹翼成形工艺
1.6.1主要原材料选择
材料选用应用较多、时间较久、工艺性能较稳定的648#树脂11和T300碳纤维。
基体材料选用648#环氧树脂,增强材料选用T300-3K碳纤维,固化剂选用质量和性能较稳定的三氟化硼单乙胺。
弹翼胶接材料,采用J一41系列结构胶。
1.6.2制定工艺流程
复合材料弹翼在研制前,确定和选用主要原材料;编制出复合材料半翼成形工艺规程和弹翼成形工艺规程;制定工艺线路等工艺文件。
复合材料弹翼研制工序见成形工艺流程简图2
1.6.3半翼成形包括
1)制定铺层表2)铺层3)固化
1.6.4弹翼胶接工艺
胶接工艺按装配工艺规程要求,将两个对称型面的半冀零件清理干净以后,在弦平面贴入J一47A结构胶,然后将左右两个半翼对合不错位主副接头放里标准定位块,擂人定位销,同时检查预埋通气孔是否畅通,不能有堵塞。
弹翼放入组合模具内检查接头定位块及插销是否到位,确保弹翼胶接固化以后,装配尺寸稳定
2弹翼复合材料成形所遇到的问题及拟采用的解决方法
弹翼在试生产的初期,突出的质量问题是弹翼主接头连接孔的孔径、弹翼接头尺寸公差、弹翼水平测量点等,往往因这些质量问题影响产品交付和使用,为此必须逐一采取措施解决。
2.1控制定位基准
对于弹翼在成型过程中以什么作为定位基准。
确保弹翼主要尺寸符合设计要求一直有不同的认识,规纳起来有三种不同的认识和看法。
(1)以弹翼前缘边为基准;
(2)以弹翼主接头端面为基准;
(3)以弹翼连接孔作为定位基准。
骨架铺层固化成型,弹翼组装胶接,以及弹翼配孔,各道生产工序定位基准必须统一,否则工序间质量失去控制,最终弹翼产品外形尺寸和接头尺寸公差难以保证。
因此弹翼的定位基准与控制十分重要。
弹翼在生产中,模具上的零件、档条每次需要拆卸。
由于成型模具周边框的档条是活动块,必然存在一定间隙;另一个问题复合材料骨架在成型加压固化过程中,在成型压力的作用下,向模具四周产生挤压力,这就导致周边框的档条向外挤涨。
由于上述两个原故,弹翼外形尺寸和主接头尺寸公差难以准确控制,特别是主接头的孔边距尺寸更难掌握。
所以,
(1)和
(2)两条作为产品的定位基准是很难控制的。
每件产品的偏差量均不相同,只有主接头的螺栓孔作为定位基准是可行的,因为定位芯棒装在模具上,一般不动,所以不会偏移,是准确的。
因此,确定弹翼在生产中各遭工序的控制尺寸均以螺栓孔作为定位基准是可行且合理的。
2.2控制芯棒与螺孔的配合间隙
弹翼主接头螺栓孔是钛合金材质,是预埋在产品之中,成型之后通过机械加工方式进行钻扩孔,从而保障孔的精度要求,否则为螺栓孔不合格。
弹翼试生产初期,由于预埋螺栓孔与定位芯棒的间隙控制量不严格,造成预埋螺栓孔偏移量过大,导致弹翼扩孔的尺寸公差不符合要求,造成了弹翼产品报废。
这个问题拟从两方面来解决,一方面对每一个螺孔严格检验,对芯棒定期检测,不符合尺寸要求的及时更换;另一方面,将预埋螺孔的孔径缩小,给最终弹翼配钻孔增加富裕量,使芯棒与螺孔的配合间隙得到有效控制,弹翼的配钻孔质量得到有效保证。
2.3控制主接头槽宽尺寸
弹翼主接头槽宽尺寸是交付和使用的重要尺寸,必须符合设计要求,因此,在弹翼成型过程中进行控制也是十分重要的。
为保证弹翼接头尺寸符合要求,在弹翼胶接组装过程中,需放置一个标准装配定位块来控制弹翼主接头的槽宽尺寸。
这个标准装配块起两个质量控制作用,其一是保证弹翼主接头槽宽尺寸;其二是确保弹翼对接螺栓孔同芯定位和最终弹翼配钻孔的质量。
弹翼主接头槽宽尺寸公差不仅影响到钻模孔工装、检验工装的对接公差要求,更重要的是直接影响到与弹体对接的尺寸公差要求,所以在弹翼生产过程中必须严格控制。
2.4胶接质量控制
弹翼胶接工序是生产中的关键工序。
是生产质量控制的重要环节。
弹翼研制和试生产的最初阶段,弹翼组合使用的工装很简陋。
组装时的周边使用几块型面压板,放置在弹翼胶接的上表面,采用弓形夹加压方式。
由于弹翼胶接面上的压力不均匀,致使胶接质量和弹翼水平测量点控制不稳定,甚至出现过压伤弹翼的现象,为此,拟使用一套弹翼组合的形芯压力工装。
该套形芯压力工装具有以下优点:
(1)采用形芯加力原理,能确保胶接面压力均匀,非胶接面不受力,所以不会出现因压力过大而压伤弹翼的问题,弹翼的胶接质量得到保证。
(2)操作简便工效提高。
组装弹翼明显地提高了装模速度。
(3)装模时任何操作人员都能准确对位,确保弹翼外形尺寸符合质量要求。
2.5弹翼水平测点的控制
弹翼水平测量点是产品检验和产品交付使用的重要指标,也是我们进行产品质量控制项目的指标之一,往往其它项目检验均合格,唯独水平测量点不合格而影响产品交付使用。
弹翼水平测量点不合格的因素一般有下列情况:
(1)碳/环氧骨架翘曲变形;
(2)存放不当产生变形;
(3)胶接固化过程中,压力和温度控制不当产生变形。
固化压力和温度是复合材料弹翼胶接的重要条件,但也是弹翼变形的重要因素。
复合材料是属于各向异性材料,在一定温度和压力条件下,变形量受材料铺层方向和产品厚薄影响,另外材料各个方向的膨胀系数也不相同,因此,复合材料变形量极难掌握。
复合材料热应力公式为:
,因此我们必须通过实验来不断增强对复合材料矫形的经验。