第三节冷轧工艺.docx
《第三节冷轧工艺.docx》由会员分享,可在线阅读,更多相关《第三节冷轧工艺.docx(50页珍藏版)》请在冰豆网上搜索。
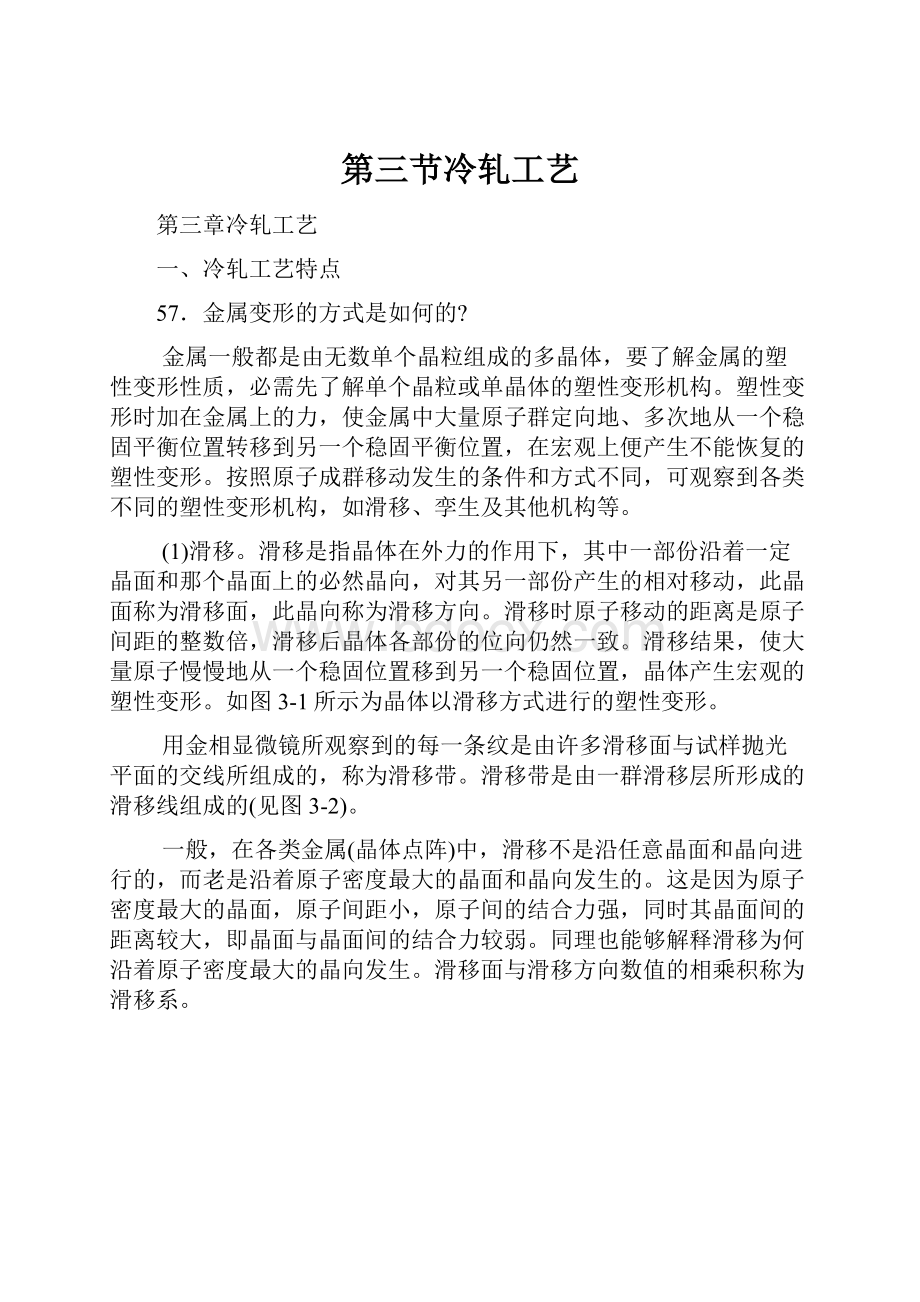
第三节冷轧工艺
第三章冷轧工艺
一、冷轧工艺特点
57.金属变形的方式是如何的?
金属一般都是由无数单个晶粒组成的多晶体,要了解金属的塑性变形性质,必需先了解单个晶粒或单晶体的塑性变形机构。
塑性变形时加在金属上的力,使金属中大量原子群定向地、多次地从一个稳固平衡位置转移到另一个稳固平衡位置,在宏观上便产生不能恢复的塑性变形。
按照原子成群移动发生的条件和方式不同,可观察到各类不同的塑性变形机构,如滑移、孪生及其他机构等。
(1)滑移。
滑移是指晶体在外力的作用下,其中一部份沿着一定晶面和那个晶面上的必然晶向,对其另一部份产生的相对移动,此晶面称为滑移面,此晶向称为滑移方向。
滑移时原子移动的距离是原子间距的整数倍,滑移后晶体各部份的位向仍然一致。
滑移结果,使大量原子慢慢地从一个稳固位置移到另一个稳固位置,晶体产生宏观的塑性变形。
如图3-1所示为晶体以滑移方式进行的塑性变形。
用金相显微镜所观察到的每一条纹是由许多滑移面与试样抛光平面的交线所组成的,称为滑移带。
滑移带是由一群滑移层所形成的滑移线组成的(见图3-2)。
一般,在各类金属(晶体点阵)中,滑移不是沿任意晶面和晶向进行的,而老是沿着原子密度最大的晶面和晶向发生的。
这是因为原子密度最大的晶面,原子间距小,原子间的结合力强,同时其晶面间的距离较大,即晶面与晶面间的结合力较弱。
同理也能够解释滑移为何沿着原子密度最大的晶向发生。
滑移面与滑移方向数值的相乘积称为滑移系。
图3—1晶体滑移示用意
图3-2单晶体的滑移带、滑移线和滑移层示用意
金属的3种常见晶格的主要滑移面、滑移方向和滑移系如表3-1所示。
(2)孪生(孪晶、双晶)。
金属的塑性变形除以滑移方式进行外,孪生也是其重要方式之一。
孪生是晶体在切应力的作用下,其一部份沿某必然晶面和晶向,按必然的关系发生相对的位向移动,其结果使晶体的一部份与原晶体的位向处于相彼此称的位置,如图3-3所示。
表3-1金属的主要滑移面、滑移方向和滑移系
图3-3晶体的孪生示用意
在孪生变形时,所有平行于孪生面的原子平面都朝着一个方向移动。
每一晶面移动距离的大小与它们距孪生面的距离成正比。
每一晶面与相邻晶面的相对移动值等于点阵常数的几分之一。
孪生变形后,晶体的变形部份与未变形部份以孪生面为对称面形成对称。
孪生变形是不是出现,与晶体的对称性有紧密关系。
面心立方晶体组织的金属(如镍、铝等),由于对称性高,容易滑移,孪生变形不常见,只在少数情形下(如低温变形)才能见到。
体心立方晶体组织的金属(如α铁、铬、钼等),在高速变形(如冲击)或在低温拉伸时,常常出现孪生。
例如铁在低温受冲击载荷时,可发生孪生。
密排六方晶体组织的金属,其对称性较差,滑移系少,当晶体取向无益于滑移时,孪生便成为塑性变形的主要形式。
孪生的进行进程往往是突变式的,并可听到特有的干裂声,在某些情形下会使晶体产生间隙,降低其密度。
除滑移和孪生外,在塑性变形中由于各个晶块(镶嵌块)彼此转动的结果,晶体产生变形,并破坏晶块间的联系和在晶块间界上形成显微破坏。
由于变形条件的不同,这些破坏可能愈合,也可能进展为宏观破坏。
总之,滑移是金属塑性变形的主要方式,金属在冷塑性变形时通过滑移变形,使晶粒伸长、镶嵌块碎化、晶格歪扭增多,致使金属变形抗力增加。
58.什么叫加工硬化。
如何消除?
带钢在冷轧后,晶粒被压扁、拉长(见图3—4)、晶格歪扭畸变、晶粒破碎,使金属的塑性降低、强度和硬度增高,这种现象叫做加工硬化。
图3—4冷轧前后晶粒形状转变
a-变形前的退火状态组织;b-变形后的冷轧变形组织
冷轧带钢加工硬化后提高了钢的变形抗力,给带钢继续冷轧带来困难。
为了消除加工硬化,大多数带钢必需在加工进程中进行再结晶退火(软化退火或中间退火)。
再结晶退火(软化退火或中间退火)时,将带钢加热到再结晶温度(碳钢一般为450~500℃)以上150~200℃,保温一按时刻,然后在空气或炉中冷却。
再结晶退火时钢的内部组织转变进程,分为回答、再结晶和晶粒长大几个阶段。
金属加工硬化后,处于组织不稳固状态,即处于高能状态,因而它本身就有自发恢复变形前组织的偏向。
在回答阶段中,冷轧变形后形成无数的位错大部份密集在晶界上,随着加热进程的进行,金属内部原子活动能力增大,使位错移动、归并或从头排列,使晶格畸变减小,金属的应力能够消除,可是金属的力学性能较回答前略有下降。
当继续加热时,由于位错聚集在晶粒间界上,这些位错移动归并,并形成新的晶核,随着温度的继续升高,晶核逐渐长大形成新的晶粒。
这时晶粒的畸变大大减小,原子排列规则,破碎的晶粒变成整齐的晶粒,长晶粒变成等轴晶粒,从而致使带钢力学性能恢复到加工前的状态,这就完成了再结晶进程。
而以完全实现回答再结晶的温度称为再结晶温度。
图3-5是冷加工后在加热时组织性能的转变示用意。
冷轧带钢的再结晶退火,一般分慢速加热退火和快速加热退火两种。
慢速加热退火一般用燃煤(气)退火炉或罩式退火炉进行;快速加热退火一般采用持续退火炉。
图3-5冷加工后金属在加热时组织性能的转变
δ-伸长率;σb-抗拉强度
59.冷轧使带钢的组织发生什么转变?
钢在常温下进行冷轧,将完全发生加工硬化现象。
钢在冷轧中组织发生如下转变:
(1)晶粒被拉长。
冷轧中,随着带钢厚度的改变,其内部的晶粒形状也发生相应的转变,即都沿轧制方向(最大主变形方向)被拉长、拉细或压扁,如图3-4所示。
晶粒被拉长的程度取决于变形程度,变形程度越大,晶粒形状转变也越大。
在晶粒被拉长的同时,金属中的夹杂物也在延伸方向拉长或拉碎,呈链状排列,这种组织称为纤维组织。
变形程度越大,纤维组织越明显。
由于纤维组织的存在,变形金属的横向(垂直于延伸方向)力学性能降低。
(2)亚结构。
亚结构是金属冷轧后,其各个晶粒被分割成许多单个的小区域。
每一个小区域称为晶块。
这些区域的内部位错密度很低,晶格的畸变很小。
而在这些小区域的边界上存在有大量位错组成的位错缠结。
(3)变形织构。
如图3-6a所示,金属的多晶体是由许多不规则排列的晶粒所组成的。
但在冷轧进程中,当达到必然的变形程度后,由于在各晶粒内晶格取向发生了转动,其特定的晶面和晶向趋于排成必然方向(图3-66),从而使原来位向紊乱的晶粒出现有序化,并有严格的位向关系。
金属所形成的这种组织结构叫做变形织构。
板结构是某一特定晶面平行于板面,某一特定晶向平行于轧制方向。
图3—6多晶体晶粒的排列情形
a-晶粒的紊乱排列;b-晶粒的整齐排列
60.冷轧使带钢的性能发生什么转变?
钢的性能是与钢的组织紧密相关的。
冷轧时,钢的组织要发生转变,因此钢的性能也要改变。
(1)力学性能的改变。
由于在冷变形中产生晶格畸变、晶粒拉长和细化、出现亚结构和产生不均匀变形等,金属的变形抗力指标(屈服极限、强度极限、硬度等),随变形程度的增加而升高。
又由于在变形中产生晶内和晶间的破坏、不均匀变形等,金属的塑性指标(伸长率、断面收缩率等)随变形程度的增加而降低。
图3-7为碳的质量分数为%的碳钢在冷拔时力学性能的转变图。
图3-7碳的质量分数为%的碳钢冷拔时力学性能的转变
σb-强度极限;σs-屈服极限;σp-比例极限;σyn-弹性极限;ψ-断面收缩率;
δ10-伸长率;HB-布氏硬度
(2)理化性质的改变。
变形金属的密度降低。
由于在冷变形进程中,晶内和晶间物质的破碎,变形金属内产生大量的微小裂纹和间隙,使金属密度降低。
例如,退火状态钢的密度为7.865g/cm3,而经冷变形后则降低到7.78g/cm3。
金属的导电性降低。
随着变形程度的增加,晶向和晶内的破坏,使单位电阻增加。
金属的导热性降低。
冷变形可改变金属的磁性。
磁饱和大体上不变,矫顽力和磁滞增大,而金属的最大磁导率则降低。
冷变形使金属耐蚀性降低。
金属产生各向异性,即材料的不同方向上具有不同的性能。
这是由于冷变形后出现了纤维组织和织构。
由于晶粒及晶间物质(杂质等)沿着变形方向被拉长,带钢在横向(垂直于纤维方向)的力学性能低于其纵向(平行于纤维方向)。
因织构的出现而形成的各向异性,有其不利的一面,但在必然条件下也可带来有利的效果。
例如,若对具有织构的薄板进行冲压时,则常使加工后的产品的边缘带有波形,突出的波形部份称为“制耳”,从而使产品的废品率和切边损失增加。
相反,铁的磁化性能与晶向有关,若将硅钢片制成某一特定晶向的织构,用它作变压器的铁芯,与无织构硅钢片比较,它具有专门大的优越性。
因此,目前工业上大量生产单取向硅钢片。
61.冷轧工艺有哪些特点?
冷轧带钢的轧制工艺特点有以下3点:
(1)带钢在轧制进程中产生不同程度的加工硬化。
加工硬化超过必然程度后,带钢因过度硬脆而不适于继续轧制。
因此带钢经冷轧必然的道次(即完成必然的冷轧总压下量)以后,往往要经软化热处置(再结晶退火等),使轧件恢复塑性,降低变形抗力,以便继续轧薄。
在冷轧生产进程中,每次软化退火之前完成的冷轧工作称为一个“轧程”。
在必然轧制条件下,钢质愈硬、成品愈薄,所需的轧程愈多。
(2)冷轧进程必需采用工艺冷却和润滑。
实验表明,冷轧带钢的变形功约有84%~88%转变成热能,使带钢与轧辊的温度升高,故须采用冷却办法。
辊面温度太高会引发工作辊淬火层硬度下降,影响带钢的表面质量和轧辊寿命。
辊温的升高和辊温散布不均匀会破坏正常的辊形,直接影响带钢的板形和尺寸精度。
同时,辊温太高也会使冷轧工艺润滑剂失效(油膜破裂),使冷轧不能顺利进行。
综上所述,为了保证冷轧的正常生产,对轧辊和带钢应采取有效的冷却与调节辊温的办法。
水是比较理想的冷却剂,油的冷却能力则比水差得多。
因此大多数生产轧机都用以水为主要成份的冷却剂。
冷轧采用工艺润滑的主要作用是减小金属的变形抗力,如此在已有的轧性能力条件下实现更大的压下,还可使轧机生产出更薄的产品。
图3-8为采用不同润滑剂的轧制效果比较。
由图可知,当冷轧机工作辊直径为88mm,带钢原始厚度为0.5mm,用水做润滑剂时,轧至厚度为0.18mm左右就难以再轧薄了;而用棕榈油做工艺润滑剂时,则可用4道次轧至O.05mm的厚度。
另外,工艺润滑对降低轧辊的温升也起到良好的作用;采用工艺润滑还可起到避免金属粘辊的作用。
常常利用的工艺润滑剂有乳化液、各类黏度的矿物油(机油等)和动、植物油(牛油、菜油、棕榈油等)。
(3)冷轧中采用张力轧制。
张力轧制就是带钢在轧辊中轧制变形是在必然前张力和后张力作用下进行的。
图3-8不同润滑剂的轧制效果比较
l-水;2-矿物油;3-棕榈油;4-合成棕榈油;5-干辊轧制
张力的作用主如果:
避免带钢在轧制进程中跑偏(即保证正确对中轧制);使所轧带钢维持平直(包括在轧制进程中维持板形平、直和轧后板形良好);降低金属的变形抗力,有利于轧制更薄的产品,起适当调整冷轧机主电机负荷的作用。
由于张力的转变会引发前滑与轧辊速度的改变,故其对冷轧进程有必然的自动调节作用。
通过改变卷取机或开卷机的转速、各架轧机主电机的转速和各架的压下,能够使轧制压力、张力在较大范围内转变。
生产中张力的选择主如果指选择平均单位张力σ平。
不同的轧机,不同的轧制道次,不同的品种规格,乃至不同的原料,要求有不同的σ平来适应。
当轧钢工人操作技术水平较高时,可选用σ平大些;当带钢硬脆、边部不睬想或操作不熟练时,σ平可取得小些。
按照以往的轧制经验,σ平在~σs的范围内选取。
62.冷轧工艺润滑的目的和对工艺润滑莉的要求是什么?
在冷轧中应用工艺润滑可达到下列几个目的:
(1)减小变形区接触弧表面上的摩擦系数和摩擦力,使轧制压力和能量消耗降低。
应用润滑剂可增大道次压下量和减少道次数,同时还可提高轧制速度。
(2)有润滑轧制可使轧机轧出更薄的带材。
所谓“可轧制厚度的极限”,取决于轧辊的弹性压扁。
润滑能减小摩擦系数和轧制压力,从而能轧制更薄的带材。
(3)润滑可避免金属粘(焊)在轧辊上。
(4)工艺润滑剂兼有冷却剂的功能。
润滑剂也能起洗涤剂的作用,它能保证从辊面和金属表面冲洗掉金属微粒(磨损物)和其他污垢。
(5)冷轧带钢平整中,采用润滑剂可改善金属表面粗糙度。
工艺润滑剂应知足一系列工艺、经济和劳动卫生特点的要求。
一般的大体要求如下:
(1)降低外摩擦力(摩擦系数);
(2)减少磨损并避免轧辊粘钢;
(3)保证轧材表面光洁;
(4)很高的热容(用做润滑一冷却液);
(5)成份和性质的稳固性;
(6)便于喷涂到轧辊和金属上;
(7)对金属和设备没有损害(侵蚀等);
(8)无毒性、没有难闻气味;
(9)最小污染和废水净化简单;
(10)廉价和资源丰硕(适合普遍应用)。
菜子油或豆油能知足冷轧工艺润滑的要求;棕榈油的润滑效果好,但来源欠缺,本钱昂贵;乳化液是实际生产顶用得最广的一种冷轧润滑冷却剂。
矿物油中加入其他添加剂,也可提高矿物油的润滑性能,且来源丰硕,本钱低廉。
63.冷轧工艺润滑剂有哪几种?
冷轧工艺润滑剂常采用下列几种:
(1)矿物油。
轧制中采用的矿物油有:
变压器油、12号和20号机油(2号和3号锭子油)、11号汽缸油、24号汽缸油(黏油)、28号轧钢机油(亮滑油)等。
在轧制中以纯油方式应用,或加少量防腐添加剂、洗涤剂、抗氧化剂等。
(2)植物油。
作为工艺润滑油的植物油顶用途最广的是:
棕榈油、蓖麻油、棉子油、葵花子油等。
(3)乳化液。
一种液体以细小的液滴散布在另一种液体中,形成两种液体组成的足够稳固的液体,称为乳化液。
乳化液普遍应用于各类轧制进程。
它的冷却能力比油大得多,在循环系统中可长期利用,耗油量较低,而且有良好的抗磨性能。
乳化液所用的基础油有矿物油、植物油和动物脂肪等。
常见的以矿物油和植物油(或合成产品)混合物为基础的乳化液有:
以20号或12号机油加合成脂肪酸和三乙醇胺聚合物形成的乳化液;聚合物棉子油和20号机油(配比1:
1)混合物的乳化液。
实际上,常常利用乳化油一混合物(油和乳化剂组成)制备乳化液。
乳化油由油脂化工厂供给。
在轧钢车间直接用乳化油制备乳化液。
在轧钢生产中采用的水一油乳化液,其质量分数通常在1%~10%范围内。
64.什么叫最小可轧厚度,如何使轧机轧出更薄的产品?
生产实践表明,在必然轧机上轧制某种产品时,随着带钢的逐渐变薄,压下愈来愈困难,当带钢厚度薄到某一限度后,无论如何旋紧压下螺丝或加大液压压下的压力,无论反复轧制多少道,也不可能再使产品轧薄。
这时带钢的极限厚度称为最小可轧厚度。
在轧制中,轧件与轧辊彼此作用,轧件在轧辊作用下产生塑性变形。
固然,轧件也伴有微小的弹性变形,通过轧辊后有一极小的弹性变形量恢复,增加了轧件厚度。
轧机、轧辊等受轧件的反力产生弹性变形。
如图3-9所示,厚度为H的轧件通过轧辊压下△h总,但轧辊弹性变形使轧件减少压下△h1,同时轧件出轧辊后,弹性变形恢复又使轧件压下减少△h2,结果,轧件实际压下量为:
由上式可知,当
时,轧件通过轧辊将不产生压下。
这时的轧件的厚度就叫最小可轧厚度。
图3-9轧机弹性变形对轧件尺寸的影响
生产中,一台带钢冷轧机所能轧出的最薄厚度是必然的。
如四辊轧机,工作辊直径为85~90mm,可轧出最小厚度为~0.10mm的钢带。
工作辊辊径与成品带材厚度的比例关系为:
这是最大的比例,轧制较困难,往往需增加中间退火和轧制道次,对轧辊材质的要求也更高。
一般工作辊辊径与成品带材厚度的比例关系按下式来选取或肯定:
应该指出:
带钢最小可轧厚度不单单由轧机工作辊直径这一因素所决定,还取决于金属材料的性质、张力、润滑情形、轧辊材料等。
带钢最小可轧厚度为:
按照上式分析,要想轧制厚度更薄的带钢,显然应该:
(1)有效地减小金属在轧制进程中的实际变形抗力,减小工作辊直径,采用高效率的工艺润滑剂,适当采用张力轧制,适当安排软化热处置。
(2)增加轧机的刚性,主如果要有效地减小轧辊的弹性压扁。
例如,二十辊冷轧机采用直径小达10mm的碳化钨工作辊,其弹性模量E几乎是一般合金锻钢辊的30倍,可轧制厚度小达O.001mm的极薄带钢。
二,冷轧工艺参数
65.如何用图表法求出咬入角?
轧制是利用两个旋转着的轧辊将轧件咬入辊缝而进行的。
轧辊咬入轧件是实现轧制所必需的条件。
在实际生产中,咬入是不是顺利对轧钢机的正常操作和产量有直接影响。
压下量大不易咬入。
如图3-10所示,轧制时轧件与轧辊表面接触的弧线叫咬入弧。
咬入弧所对的圆心角称为咬入角。
咬人角由压下量肯定。
在不同轧制条件下,最大允许咬人角是不同的,其大小与轧辊表面和轧件的表面状态、轧制温度和轧辊转速等因素有关,即与轧辊和轧件间摩擦系数有关。
当轧辊的线速度在~2.5m/s时,在表面粗糙的轧辊上冷轧,最大允许咬人角为5º~6º;在表面滑腻带润滑的轧辊上冷轧,咬人角为3º~4º。
图3-10△h-a-D图表
由图3—10可知,咬入角的计算公式为:
或
式中△h——压下量(Δh=H-h),mm;
D——轧辊工作直径,mm;
a——咬入角。
当咬入角大于最大允许的咬入角时,轧件不能咬入。
a、△h和D三者之间的关系可用图表表示出来(见图3—10)。
若是上面三值中二者为已知,则另一值能够迅速地借此图表求得。
例如,已知D=165mm、a=5°时,由图可求得△h=0.627mm。
已知D=460mm、Δh=29mm时,由图可求出α=20°20ˊ。
66.影响冷轧轧制压力的因素有哪些?
影响轧制压力的因素很多,大体上能够分为两大类。
第一类是影响金属变形阻力的,其中有金属材料的化学成份、变形温度与变形程度,金属变形阻力增高,将使压力加大。
第二类是影响应力状态条件的因素,其中有外摩擦(即摩擦系数)、轧件及轧辊直径、张力等。
下面别离说明上述各因素的影响:
(1)钢种不同,即金属材料化学成份不同,材料本身力学性能不同,因此变形阻力不同。
(2)变形程度的影响也就是加工硬化的影响。
金属塑性变形时,其形状转变能量大部份用于塑性变形,以热的形式存在;另外一部份则产生晶格扭转、位错等,内能增高,这部份保留在金属中的能量叫做残留畸变能,此能量将使金属的变形阻力增加,出现加工硬化现象。
在冷轧时,轧制是在再结晶温度以下进行的,其组织性能不能恢复,产生了强化,则变形阻力将随变形程度增加而增加。
(3)随着变形温度的升高,变形阻力降低。
随着变形速度的提高,变形阻力将增加。
可是,对冷轧来讲,变形温度和变形速度对变形阻力的影响不很显著。
(4)摩擦力越大,压力也越大。
粗糙表面轧辊的摩擦系数比滑腻表面轧辊高,所以压力也大。
(5)轧件厚度和轧辊直径的影响。
随着轧件厚度的减薄,轧制压力增加。
在其他条件相同情形下,轧辊直径越小,轧制压力越低。
这一方面是接触面积减小使轧制力减小,另一方面是单位压力减小而使轧制压力减小,所以在冷轧薄带时,为了降低轧制压力,一般均采用小直径轧辊,如轧制极薄带材时,轧辊直径乃至小到2mm。
现在用增加支撑辊的办法来提高其刚性。
(6)张力的影响。
带钢的前后张力都使单位压力降低,且后张力影响更为明显。
由于存在张力,变形区内金属在轧制方向产生附加拉应力,此拉应力引发轧制时三向压应力状态的水平方向主应力减小,从而降低了单位压力。
因中性面偏向带钢出口,故后张力影响大于前张力。
67.轧制压力与变形抗力有何区别?
轧制压力是指金属轧制变形时所需的总压力,它是选择和肯定轧钢设备的主要数据。
变形抗力是指金属抵抗塑性变形的能力,它的单位是Pa。
变形抗力的大小取决于金属中原子间的结合力。
这与钢种、变形温度、变形程度和变形速度有紧密关系。
轧制压力的大小,除与钢种的变形抗力有关之外,还与变形时的受力方式、轧件形状尺寸和摩擦条件等有关。
68.金属塑性和金属柔软性是一回事吗?
金属所以能轧制,主如果由于金属具有塑性这一特点。
金属塑性是指金属在外力作用下,能肯定地发生永久变形而不破坏其完整性的能力。
金属塑性的大小,可用金属在断裂前产生的最大变形程度来表示。
它表示压力加工时金属塑性变形的限度,所以也叫塑性极限,一般通称塑性指标。
金属的塑性,不仅受金属内在的化学成份和组织结构的影响,也和外在的变形条件有紧密关系。
同一金属或合金,由于变形条件(拉伸或紧缩等)不同,可能表现有不同的塑性,乃至由塑性物体变成脆性物体,或由脆性物体变成塑性物体。
例如,受单向拉伸的大理石是脆性物体,但在较强的静水压力下(三向压应力)紧缩时,却能产生明显的塑性变形而不破坏。
金属柔软性是反映金属的软硬程度,它用变形抗力的大小来衡量。
因此,不能把塑性和柔软性混淆起来,不要以为变形抗力小的金属塑性就好,或变形抗力大的金属塑性就差。
例如,室温下奥氏体不锈钢的塑性专门好,可经受专门大的变形而不破坏,但其变形抗力却专门大;过热和过烧的金属和合金的塑性很小,乃至完全丧失塑性变形的能力,而其变形抗力也很小;也有些金属塑性专门好,变形抗力又小,如室温下的铅等。
69.什么叫附加应力和残余应力,它们对金属性能有何影响?
由于各类因素(如摩擦、温度不均匀或轧辊变形等)造成轧件变形不均匀时,在金属内部就会引发内应力。
金属在轧制进程中产生的这种内应力称为附加应力;轧制后残余在金属内部的附加应力称为残余应力。
无论是附加应力仍是残余应力,其中各自都包括拉应力和压应力,二者同时存在,且彼此平衡。
其中拉应力更为有害,当其值超过强度极限时,轧件就会产生裂纹。
由于变形和应力散布不均匀,单位变形力升高,则可能在轧件中较早达到金属的强度极限而发生破坏,因此使塑性降低。
附加应力会使变形能量消耗增加,单位变形力增高。
另外,应力不均匀散布,将使轧件内实际的应力散布情形与大体应力有专门大不同,使主应力状态发生转变,可能使单位变形力升高。
若轧件中存在残余应力,会使轧件的力学性能降低,另外还要使轧件形状弯曲或起皱纹,严峻时将产生裂纹或破断而造成废品。
在实际生产中,力求变形和应力均匀散布,以减少附加应力和残余应力。
例如,在冷轧薄板时,由于轧辊中部产生的弹性弯曲与压扁较大,故应将轧辊磨成凸形。
70.如何肯定冷轧时的带钢变形阻力?
冷轧时,由于存在加工硬化现象,在计算冷轧薄板平均单位压力时,轧件材料变形阻力(对冷轧亦可称为屈服极限)需按考虑加工硬化后的来选用。
由于存在加工硬化的影响,各道次的变形阻力不仅与各道次变形程度有关,而且还与前面各道次的总变形程度有关。
对各道次来讲,沿接触弧上金属变形阻力也是转变的,出口处比入口处要大。
计算时一般把变形区作为圆弧(或抛物线)转变来计算平均总变形程度ε总,按此平均总变形程度来查出变形阻力(即σ。
平均总变形程度ε总用下式计算:
例题:
由退火原料开始轧制,带钢原始厚度为1.85mm,轧制0.50mm的产品,轧制道次为两道。
Q215·F钢种的加工硬化曲线如图3-11所示。
第1道:
ho=1.85mm,h1=1.0mm,Δh=0.85mm,由于为退火状态进行轧制,故入口压下率ε。
为零,出口压下率为:
平均总压下率ε总为:
ε总=ε0+ε1=×0+×46%=28%由图3-11查出对应于;ε总=28%的σ=490MPa。
图3-11Q215·F钢种的加工硬化曲线
1-纵向;2-横向
第2道:
入口总压下率为46%,h2=,出口总压下
率为:
第2道平均总压下率为:
对应于ε总为62%的σ=700MPa。
若多道次轧制,计算方式相同。
71.计算冷轧轧制压力时如何选用摩擦系数?
冷轧时的摩擦系数与采用的润滑剂及轧辊表面状况有关,可按表3—2选择。
表3-2在研磨的轧辊上轧制冷轧钢板、钢带时的摩擦系数
轧材品种
润滑剂
摩擦系