机械制造专业毕业论文离心机主轴加工工艺规程设计.docx
《机械制造专业毕业论文离心机主轴加工工艺规程设计.docx》由会员分享,可在线阅读,更多相关《机械制造专业毕业论文离心机主轴加工工艺规程设计.docx(17页珍藏版)》请在冰豆网上搜索。
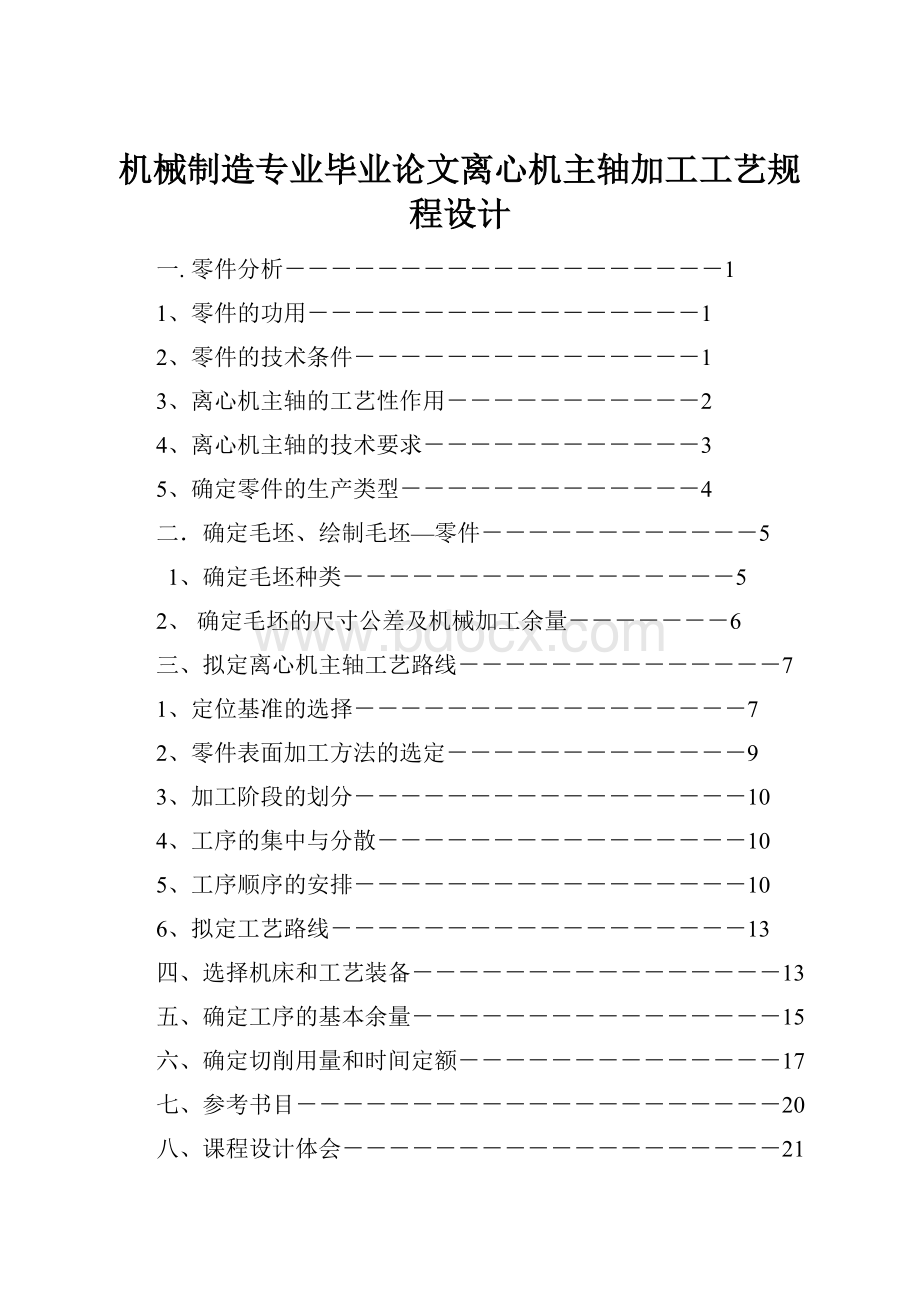
机械制造专业毕业论文离心机主轴加工工艺规程设计
一.零件分析-------------------1
1、零件的功用-----------------1
2、零件的技术条件---------------1
3、离心机主轴的工艺性作用-----------2
4、离心机主轴的技术要求------------3
5、确定零件的生产类型-------------4
二.确定毛坯、绘制毛坯—零件------------5
1、确定毛坯种类-----------------5
2、确定毛坯的尺寸公差及机械加工余量-------6
三、拟定离心机主轴工艺路线--------------7
1、定位基准的选择-----------------7
2、零件表面加工方法的选定-------------9
3、加工阶段的划分-----------------10
4、工序的集中与分散----------------10
5、工序顺序的安排-----------------10
6、拟定工艺路线------------------13
四、选择机床和工艺装备----------------13
五、确定工序的基本余量----------------15
六、确定切削用量和时间定额--------------17
七、参考书目---------------------20
八、课程设计体会-------------------21
一、零件分析
1、零件的功用
离心机主轴用来支持离心器机,安装各种零件,使离心机转动,利用离心机转子高速旋转产生的强大的离心力,加快液体中颗粒的沉降速度,把样品中不同沉降系数和浮力密度的物质分离开。
离心机主轴是一种高速回转轴,要满足高速旋转的工作要求,故它与其他非回转件,支承件间的摩擦应尽可能小,这就需要提高离心机主轴与支座相接触表面的尺寸公差等级和表面粗糙度,以减少阻力,进而减小摩擦,提高运行平稳性,减少振动,噪声,提高轴的使用寿命。
2、零件的技术条件
离心机主轴毛坯材料为45号钢。
该材料属于优质碳素钢,经热处理(淬火加高温回火)后具有良好的综合力学性能,即具有较高的的强度和较高的塑性、韧性,一般用来制作机床主轴,机床齿轮和其他受力不大的轴类零件。
主要技术要求如下:
1孔的精度:
孔的尺寸精度和位置精度直接影响该轴的配合质量,因而对轴的回转精度、传动平稳性、噪声和轴承寿命有重大关系。
轴的尺寸精度、表面粗糙度、位置精度都要求较高。
其中
150h7,
150k6,
148h7的精度等级要求最高,其尺寸精度为IT6和IT7,其余轴孔的尺寸精度为IT7或IT12。
表面粗糙度的要求分别为0.8um,1.6um,3.2um,12.5um,6.3um。
2轴孔的位置精度:
同一轴心线上各轴孔的同轴度误差会导致轴承装配时歪斜,影响轴的回转精度和轴承的使用寿命。
零件图中规定:
a、轴肩处两轴颈同轴度公差为0.02mm,表面粗糙度0.8um
b、孔
85H7的同轴度公差为0.015mm。
c、锥轴
142
的直线度公差为0.008mm,同轴度公差为
0.012mm。
3,离心机主轴的工艺性作用
分析零件图可知,离心机主轴两端面和轴面均要求切削加工,并在轴向方向上产生台阶表面,并且粗糙程度都不同,这样有利于主轴高速旋转时的各表面的应力条件,φ55mm孔、φ85mm孔、φ105mm孔的端面均为平面,因此只要防止加工过程中钻头钻偏,以保证孔的加工精度就可以了;另外,该离心机主轴除了主要工作表面(主轴两端面及外圆、内孔φ850+0.035mm和锥面)外,其余表面加工精度均低,不需要高精度机床加工,通过铣削、钻床的粗加工就可以达到加工要求;而主要工作表面虽然加工精度要求相对较高,但也可以在正常的生产条件下,采用较经济的方法保质保量地加工出来。
所以,该零件的工艺性较好。
4、离心机主轴的技术要求
根据零件图,将离心机主轴的全部技术要求列于表1中
加工表面
尺寸及偏差(mm)
公差及精度等级
表面粗糙度Ra(μm)
形位公差(mm)
主轴左端面
φ1500-0。
040
IT7
0.8
◎
φ0.02
A-B
主轴右端螺纹
M130*2—6
IT6
3.2
右端锥面
φ1420+0。
1
IT7
0.8
锥度1:
20
主轴左端内表面
φ850+0。
035
IT7
1.6
主轴右端内表面
φ850+0。
035
IT7
1.6
主轴右端内表面
φ105
6.3
φ150轴面
φ1500-0。
04
IT7
0.8
◎
φ0.02
A-B
φ148轴面
φ1480-0。
04
IT7
1.6
φ85内孔
φ850+0.035
IT7
1.6
φ55内孔
φ55
12.5
键槽
115
6.3
φ167轴
φ167
自由公差
6.3
φ150轴
φ1500-0.040
IT6
0.8
表﹤1﹥:
5、确定零件的生产类型
设计题目给定的零件时离心机主轴,要求产量为批量200件,下表为生产类型的规范
生产类型
生产纲领/(台/年或件/年)
工作地每月担负的工序数
小型机械或轻型零件
中型机械或中型零件
重型机械或重型零件
工序数/月
单件生产
≤100
≤10
≤5
不做规定
小批生产
〉100~500
〉10~150
〉5~100
〉20~40
中批生产
〉500~5000
〉150~500
〉100~300
〉10~20
大批生产
〉5000~50000
〉500~5000
〉300~1000
〉1~10
大量生产
〉500000
〉5000
〉1000
1
由以上表格可知本次生产为小批生产。
二、确定毛坯、绘制毛坯—零件合图
1、确定毛坯种类
由于该离心机主轴在工作过程中承受冲击载荷、扭转力矩,为增强离心机主轴的抗扭强度和冲击韧度,获得纤维组织,毛坯选用热扎圆钢经拔长得到。
该离心机主轴的轮廓尺寸较大,且生产类型属于小批生产,为提高生产效率和圆钢的精度,宜采用自由锻件方法制造毛坯。
2、确定毛坯的尺寸公差及机械加工余量
(1)、公差等级
由工艺手册查得该锻件的尺寸公差等级CT为8—12级,加工余量等级为普通级。
(2)零件表面的粗糙度
由零件图可知,该轴各加工表面的粗糙度均大于等于
0.8
m。
(3)、毛坯加工余量的确定
根据《锻造手册》,左右端面的加工余量确定为8mm,总长度尺寸为990+2*8=1006mm,车外圆的单边加工余量为6mm,轴直径为150+2*6=162mm,167+2*6=179mm。
为保证质量,减少加工余量,采用立式精锻机锻造,用热轧棒料经拔长得到,根据《锻造手册》,锥面部分无法通过拔长得到,轴上多处退刀槽,砂轮越程槽,锥面,键面及轴孔无法锻出,故以上各处均采用工艺敷料。
另外,为简化锻造工艺,对直径相近的台阶适当合并。
根据零件图和以上条件绘制零件毛坯图。
三、拟定离心机主轴工艺路线
1、定位基准的选择
(1)、粗基准的选择
为符合基准重合原则和能够最大限度地在一次安装中加工出多个外圆的端面,所以采用顶尖孔作为轴加工的定位基准,或采用外圆表面和顶尖孔共同作为定位基准。
加工过程中,顶尖孔应始终保持准确和清洁。
每次热处理后,以及转入下一加工阶段前,应对顶尖孔进行研磨或修整,一去除顶尖孔表面的氧化皮和其他损伤。
用外圆表面定位时,因基准面的加工和工作装夹都比较方便,一般用卡盘装夹。
但是,卡盘的定位精度较低,且工件调头车削时,两端外圆表面会产生同轴度误差,影响位置精度
(2)、精基准的选择
根据该离心机主轴的技术要求和装配要求,选择主轴左端面和左右两端φ850+0.035为精基准,零件上的很多表面都可以采用它们作基准进行加工,即遵循“基准统一”原则。
左右两端孔φ850+0.035mm的轴线是设计基准,选用其作精基准定位加工离心机主轴两端面及内孔φ55mm,实现了设计基准和工艺基准的重合,保证了被加工表面的同轴度要求,选用主轴的左端面作为精基准同样是遵循“基准统一”的原则,因为该离心机主轴在轴向方向上的尺寸多以该端面作设计基准;另外,由于离心机主轴刚性要求高,受较大的扭转力矩作用,为了避免在机械加工中产生刚性脆断,根据夹紧力应垂直于主要定位基面,并应作用在刚度大的部位的原则,夹紧力作用点不能在螺纹表面上。
选用离心机主轴左端面作精基准,夹紧可作用在离心机主轴的右端面上,夹紧稳定可靠。
2零件表面加工方法的选择
本零件的加工面由外圆,内孔,端面,外螺纹,平键等,材料为45钢,参考工艺手册,并根据离心轴零件图上各加工表面的尺寸精度和表面的粗糙度确定其加工方法选择如下:
⑴左端面:
公差等级为IT7,表面粗糙度为6.3um,加工方法为粗车→半精车
⑵右端面:
公差等级为IT6,表面粗糙度为3.2um加工方法为粗车→半精车
⑶φ150h7外圆表面:
公差等级为IT7,表面粗糙度为0.8um,采用粗车→半精车→磨削
⑷φ150k6外圆表面:
公差等级为IT6,表面粗糙度为0.8um,采用粗车→半精车→磨削
⑸φ167外圆表面:
公差等级IT9,表面粗糙度6.3um采用粗车→半精车
⑹φ150h12外圆表面:
公差等级为IT12,表面粗糙度为6.3um,采用粗车即可
⑺φ148h7外圆表面:
公差等级为IT7,表面粗糙度为1.6um,采用粗车→半精车→磨削
⑻φ1420+0。
1锥面:
公差等级为IT9,表面粗糙度为0.8um,采用粗车→半精车→磨削
⑼左右两端
85H7孔:
公差等级为IT7,内表面粗糙度为1.6um,采用粗镗→半精镗→精镗
⑽右端
105孔:
公差等级IT7,内表面粗糙度为1.6um,采用粗镗→半精镗→精镗
⑾
55孔:
公差等级IT10,表面粗糙度为12.5um,采用深钻即可
⑿右端外螺纹:
加工方法为粗车——半精车——车螺纹
⒀左端螺孔(8-M12):
加工方法为钻孔——攻丝
对轴上深孔加工应注意一下两个问题①应安排在调质以后加工,以免因调质处理变形较大而导致深孔产生弯曲变形难以纠正,引起轴高速转动的不平衡;②应安排在外圆粗车或半精车之后进行,这样可以有一个较精确的轴颈作为定位基面,从而保证孔与外圆同心,并使轴的壁厚均匀。
3、加工阶段的划分
该离心机主轴的加工质量要求较高,可将加工阶段分成粗加工、半精加工和精加工几个阶段。
(1)粗加工阶段,这一阶段的主要目的是采用大切削用量切除大部分加工余量,把毛坯加工至接近工件的最终形状和尺寸,只留下适当的加工余量。
此外,还可及早发现锻件裂缝等缺陷,以便及时修补或作报废处理。
主要包括:
先粗铣主轴左右端面,钻中心孔,使后续工序都可以采用精基准定位加工,保证其他加工表面的精度要求。
(2)半精加工阶段,这一阶段的主要目的是为精加工做好准备,尤其是做好基面准备。
对一些要求不高的表面(如左右端面和φ167外圆面),应在这一阶段完成全部加工,达到图样规定的技术要求。
(3)精加工阶段,进行离心机主轴的主轴左端内表面、主轴右端内表面、φ850+0.035mm内孔的精铣,右端锥面、φ150mm轴面、φ150轴的精磨。
4、工序的集中与分散
工序适当集中,以减少设备使用更换次数,并尽量采用通用设备,
关键工序必要时采用专用设备。
较多采用夹具,在确保质量的前
提下,尽量是生产具备较大的柔性。
5、工序顺序的安排
﹤1﹥、机械加工工序
(1)遵循“先加工基准面,再加工其他表面”原则,首先加工基准——将端面先加工,再钻中心孔,以中心孔定位车表面的外圆。
(2)遵循“先加工平面后加工孔”原则,先加工左右端面,
再以端面定位来加工各个镗孔。
(3)遵循“先加工主要表面,后加工次要表面”,先加工主要表面——车外圆各个表面及镗各个孔,后加工次要表面——铣键槽和加工各个小槽。
由于次要表面和主要表面之间往往有相互位置精度要求,因此一般应在主要表面达到一定精度后,再以主要表面定位加工次要表面。
(4)遵循“先安排粗加工工序,后安排精加工工序”原则,先安排粗加工工序,粗车外圆,粗镗孔。
后安排精加工工序,磨削外圆,精镗孔。
﹤2﹥、热处理工序
锻造后,在切削加工前宜采用正火,能提高改善轴的硬度,消除毛坯的内应力,改善其切削性能。
在粗加工后进行调质,调质处理使轴达到220-240HBS,调质处理能使主轴获得更高的综合力学性能。
在精加工之后,进行表面淬火加低温回火,提高其耐磨性和工作中承受冲击载荷的能力。
﹤3﹥、辅助工序
在粗加工和热处理后,安排校直工序;在半精加工之后,安排去毛刺处理和中间检验工序,零件表层或内部的毛刺会影响装配操作和装配质量,甚至会影响整机性能,应予以充分重视;精加工后,安排去毛刺、清洗和终检工序。
综上所述,该轴的工序的安排顺序为:
基准加工——主要表面粗加工及镗孔的粗加工——主要表面半精加工和槽的加工——热处理——主要表面的精加工。
6、拟定工艺路线
工艺路线:
下料——正火——锻造——粗车端面,打顶尖孔——粗车各外圆——热处理(调质220-240HBS)——钻深孔——切槽,镗孔——车定位面——切槽,半精车外圆,端面——中间检验——铣键槽——车螺纹——磨削外圆(含锥面)——倒角,去毛刺——最后检验
离心机主轴加工工艺过程
序号
工序名称
工艺过程
加工设备
10
下料
20
锻造
尺寸
162X1006mm,两处凸肩
179X50mm
30
热处理
正火
40
粗车端面,打顶尖孔
先粗车左端面,打顶尖孔,调头,车右端面,打顶尖孔,保证轴长度尺寸992.4mm
卧式机床C616A
50
粗车外圆
以顶尖孔定位,,粗车各外圆
卧式机床C616A
60
热处理
调质(220-240HBS)
70
钻孔
以左右外圆定位,用深孔麻花钻
55通孔
深孔钻床
80
镗孔
以外圆定位,加工好退刀槽,粗镗→半精镗→精镗
85H7和
105
镗床T612
90
车定位面
以心轴和顶尖定位,为精车定位
100
半精车端面
半精车左端面,保证尺寸991.2mm,调头,半精车右端面保证尺寸990mm
卧式机床C616A
110
半精车各外圆
卧式机床C616A
120
中间检验
检验各尺寸是否达到预定要求,以便修正
130
铣键槽
铣床
140
车螺纹
150
磨削各外圆面
重新检查各定位是否准确,用磨床磨削各外圆,并磨出1:
20的锥度
磨床MBS1320
160
最后检验
将钻深孔放在粗车和半精车之间,主要是为了在钻孔时有一个较精确地轴颈作为定位基准面,从而保证孔与外圆同心,并使轴的壁厚均匀,钻孔后镗孔,表面粗糙度搞的外圆用磨削加工,精度易保证。
四选择机床和工艺装备
1选择机床:
该零件为小批生产,应采用专用机床
1打中心孔机床Z8220B用来加工顶尖孔来进行定位
2端面加工和车外圆均可采用卧式车床C616A,可以进行粗车和
精车。
3各外圆的磨削采用外圆磨床MBS1320
4轴孔属深孔,必须采用深孔钻头加工,如采用深孔麻花钻头加工完成。
5
85H7孔轴孔的加工,粗镗,精镗采用卧式镗床T618加工.
2选择夹具
1粗车,半精车可采用自定心卡盘,尾座顶尖及其他专用家具
2轴孔加工出后,车,磨工序均采用心轴和顶尖装夹
3选择刀具
1车端面和外圆时,用硬质合金刀具YT15,这种刀具适用于碳
钢与合金钢加工中。
2镗孔采用双刃镗刀,适用于半精加工和精加工
3钻深孔采用专用的深孔麻花钻头
4磨削外圆采用平形砂轮
具体刀具尺寸如下:
⑴粗车采用前角12度,后角6度,主偏角45度,刃倾角+5度的焊接式车刀,精车采用前角11度,后角7度,主偏角90度,刃倾角8度的焊接式车刀,以上两种车刀,长度L=90-240mm,h=10-50mm,b=10-50mm。
⑵深孔麻花钻头的锋角120度,后角13度,横刀斜角45度,螺旋角25度。
⑶双刃镗刀D=50-260mm
⑷粗磨用P400X60X127AM6V35,粒度40-60,硬度L-M,使用陶瓷结合剂,精磨用P400X60X127WAK5V35,粒度60-80,硬度M-P,使用陶瓷结合剂。
4选择量具
1粗加工,半精加工选用通用量具
2左端工序尺寸
150h7,查参考文献知计量具不确定允许值u=0.012mm
3精加工工序尺寸精度要求高,通用量具使用不便,故应选用专用量具。
如外圆测量宜采用卡规,测量时要注意从相互垂直的两个方向测量。
锥面测量用专业锥度量规检验。
4各车端面尺寸测量可用分度值为0.02mm的游标尺。
五确定工序的基本余量
①
150h7,加工过程为粗车——半精车——磨削。
查参考文献取外圆磨削余量0.4mm,半精车外圆加工余量1.2mm,再根据已确定的毛坯余量6mm,可算出粗车余量为4.4mm,小于粗车一次能切削的最大余量4.49mm,故只需走刀一次。
工序名称
工序单边余量/mm
加工经济精度/mm
表面粗糙度
/
工序基本尺寸/mm
磨削
0.4
h7
0.8
150
半精车
1.2
h9
6.3
150.8
粗车
4.4
h11
>=50
153.2
锻造
2
162
φ167,加工过程为粗车——半精车,查参考文献取半精车余量1.2mm,再根据毛坯余量,算出粗车余量为4.8mm大于粗车一次能且学的最大余量4.49mm,故分两次走刀完成。
工序名称
工序单边余量/mm
加工经济精度/mm
表面粗糙度
/
工序基本尺寸/mm
半精车
1.2
h9
6.3
167
粗车
4.8
h11
>=50
169.4
锻造
2
179
其他外圆面加工余量选取方法相同,轴的尺寸大于250mm的取半精车余量1.6mm。
②通孔
55,由其加工经济精度选用通孔加工方法,用钻孔即可达到要求
③
85孔,其加工过程为:
粗镗—半精镗—精镗。
第一次粗镗至φ80mm,第二次粗镗至φ83mm,加工余量3mm,半精镗至φ84.3mm,加工余量1.3mm,精镗至φ850+0.035mm,加工余量0.7mm。
工序名称
工序余量/mm
加工经济精度/mm
表面粗糙度
/
工序基本尺寸/mm
精镗
0.7
h7
0.8
85
半精镗
1.3
h9
6.3
84.3
粗镗
3
h11
>=50
83
④
105孔,其加工过程为:
粗镗—半精镗—精镗。
第一次粗镗至φ100mm,第二次粗镗至φ103mm,加工余量3mm,半精镗至φ104.3mm,加工余量1.3mm,精镗至φ105mm,加工余量0.7mm。
工序名称
工序余量/mm
加工经济精度/mm
表面粗糙度
/
工序基本尺寸/mm
精镗
0.7
h7
0.8
105
半精镗
1.3
h9
6.3
104.3
粗镗
3
h11
>=50
103
六确定切削用量和时间定额
⑴加工外圆柱面φ150,选用机床C616A,切削材料为45钢,用YT15,查参考文献,由经验公式
T=60,Cv=235,Xv=0.15,Yv=0.45,m=0.2,查《机械加工工艺设计手册》P433得知:
f=0.8~1.2mm/r取f=0.81mm/rap=2.5mm,Vc=100.4m/min,
机床转速n=1000Vc/πd=1000x100.4/3.14x150r/min=213.16r/min,取n=215r/min,实际切削速度Vc=nπd/1000=101.3m/min
根据切削用量与刀具耐用度的关系可知,影响最小的是ap,其次是f,最大是V,这是因为切削温度的影响最大,温度升高,刀具磨损加快,寿命明显下降。
所以在刀具耐用度一定的情况下,为提高生产率,选择切削用量的基本原则是:
首先应选取尽可能大背吃刀量;其次要在机床动力和刚度允许的条件下,同时又满足已加工表面粗糙度要求的情况下,选取尽可能大的进给量;最后根据公式确定最佳切削速度。
⑵时间定额的确定
时间定额是在一定生产条件下,生产一件产品或完成一道工序所需消耗的时间,由基本时间按Tj,辅助实际Tf,布置工作地时间Tfw,休息和生理需要时间Tx,准备与终结时间Tz组成。
⑴计算基本时间:
150外圆,走刀一次T1=(140+475)/nf=615/215*0.81min=3.5min,
148,
130,
167走刀两次T2=(295+80)*2/nf=4min,
.粗镗φ85h7孔至φ83mm步骤如下:
(1)确定进给量。
根据参考文献[2]表5-4得,取f=0.56。
(2)确定切削速度Vc。
按表5-113,取Vc=25m/min。
(3)确定机床主轴的转速n。
n=(100Vc)/(3.14×d)=(1000×25)/(3.14×83)r/min
=96r/min
根据参考文献[2]表5-4,按机床实际转速n=142r/min.
(4)计算基本时间Tj
被加工孔长度l=120mm
查表的切入量y=5.7mm,取y=6mm,切出量△=4mm。
Tj=(l+y+△)/(nf)=(120+6+4)/(96×0.56)mm
=2.4min
(5)确定辅助时间Tf
查参考文献[2]表5-114得,变换刀架的时间为0.05min,变速或变换进给量的时间为0.02min,启动和调节切削液的时间为0.05min,共计Tf=0.12min。
3.半精镗φ85h7孔至φ84.3mm
方法同上,惨参考文献[2]表5-114的,被吃刀量ap=0.4,选进给量f=0.8mm/r,机床转速为n=285r/min,切削速度Vc=15r/min,基本时间Tj=0.8min辅助时间Tf=0.1min。
4.精镗φ85h7孔
查表5-117,被吃刀量ap=0.3mm,选进给量f=0.5mm/r,主轴转速n=142r/min,切削速度为Vc=11r/min,基本时间Tj=1.6min,辅助时间Tf=0.22min。
八、参考书目:
1、《机械制造技术基础》主编:
陆名彰、胡忠举长沙:
中南大学出版社,2004年8月
2、《机械制造技术基础课程设计指导教程》主编:
邹青北京:
机械工业出版社,2004年9月
3、《工程材料及应用》主编:
周凤云武汉:
华中科技大学出版社,2004年9月
5、《机械加工工艺基础》主编:
金问楷北京:
清华大学出版社,1990年9月
七、课程设计体会:
通过上个学期机械原理的课程设计,我对课程设计该怎么做有了一定的了解。
但是这次课程设计与机械原理的有很大的不同,在开始做的时候仍有一种不知该如何下手的感觉。
然后我就到图书馆、网络上查询资料,虽然资料有限,但在资料和课本指导下,按着上面的步骤一步步的做,慢慢的指导怎么做了。
这次课程设计并不是真的要我们自己设计东西出来,而是让我们掌握轴类零件的加工工艺过程。
通过这次课程设计,我们对这门课程上的知识又一次的加深和巩固,上课时所学的机械制造的知识,考试考完后有很多都已经忘了,通过这次的巩固学习,相当于系统的有看了一下课本。
对学好我们的专业打好了基础。
锻炼了我们自学的能力、查资料的能力。