烟气脱硫脱硝一体化技术研究进展.docx
《烟气脱硫脱硝一体化技术研究进展.docx》由会员分享,可在线阅读,更多相关《烟气脱硫脱硝一体化技术研究进展.docx(15页珍藏版)》请在冰豆网上搜索。
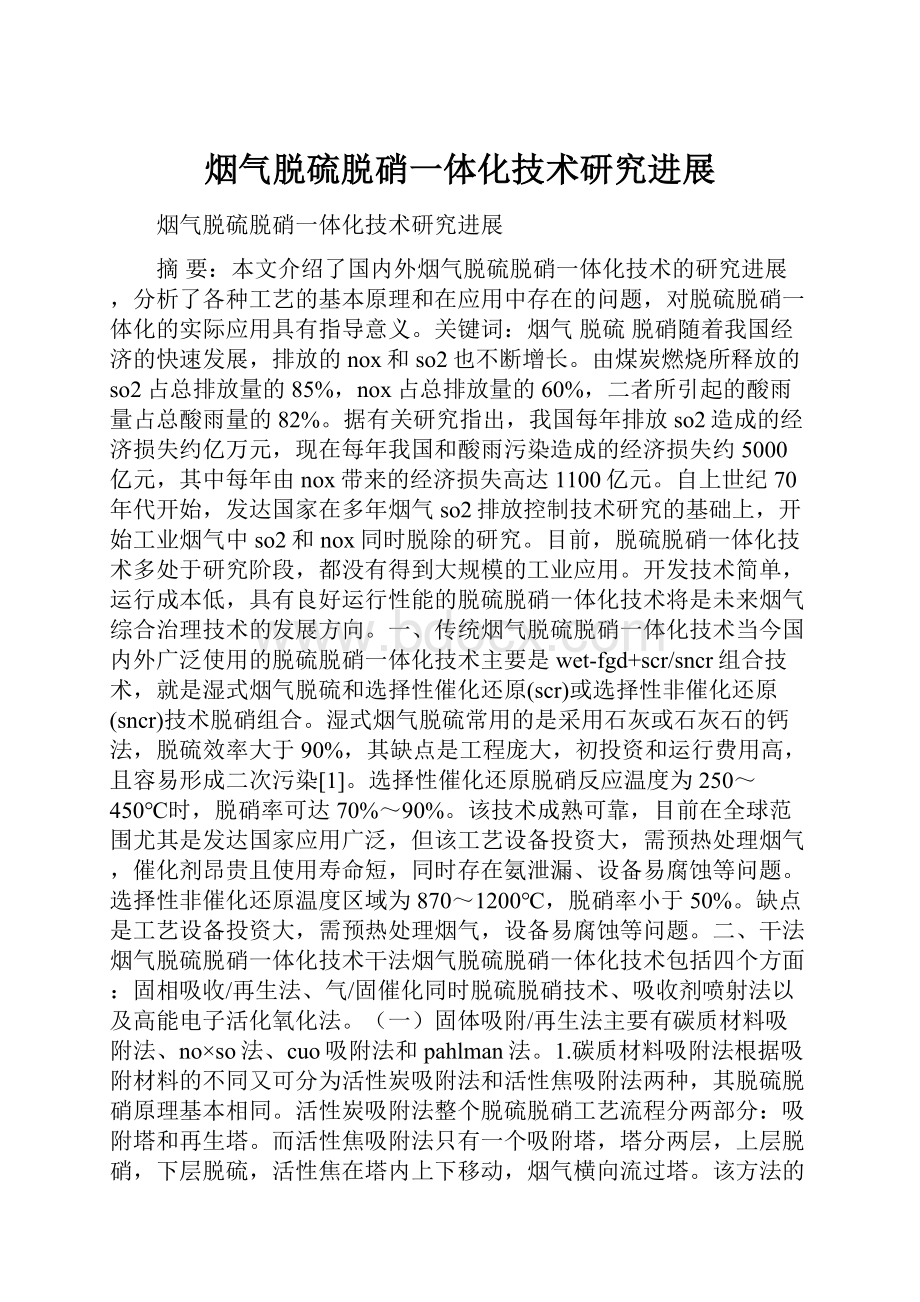
烟气脱硫脱硝一体化技术研究进展
烟气脱硫脱硝一体化技术研究进展
摘要:
本文介绍了国内外烟气脱硫脱硝一体化技术的研究进展,分析了各种工艺的基本原理和在应用中存在的问题,对脱硫脱硝一体化的实际应用具有指导意义。
关键词:
烟气脱硫脱硝随着我国经济的快速发展,排放的nox和so2也不断增长。
由煤炭燃烧所释放的so2占总排放量的85%,nox占总排放量的60%,二者所引起的酸雨量占总酸雨量的82%。
据有关研究指出,我国每年排放so2造成的经济损失约亿万元,现在每年我国和酸雨污染造成的经济损失约5000亿元,其中每年由nox带来的经济损失高达1100亿元。
自上世纪70年代开始,发达国家在多年烟气so2排放控制技术研究的基础上,开始工业烟气中so2和nox同时脱除的研究。
目前,脱硫脱硝一体化技术多处于研究阶段,都没有得到大规模的工业应用。
开发技术简单,运行成本低,具有良好运行性能的脱硫脱硝一体化技术将是未来烟气综合治理技术的发展方向。
一、传统烟气脱硫脱硝一体化技术当今国内外广泛使用的脱硫脱硝一体化技术主要是wet-fgd+scr/sncr组合技术,就是湿式烟气脱硫和选择性催化还原(scr)或选择性非催化还原(sncr)技术脱硝组合。
湿式烟气脱硫常用的是采用石灰或石灰石的钙法,脱硫效率大于90%,其缺点是工程庞大,初投资和运行费用高,且容易形成二次污染[1]。
选择性催化还原脱硝反应温度为250~450℃时,脱硝率可达70%~90%。
该技术成熟可靠,目前在全球范围尤其是发达国家应用广泛,但该工艺设备投资大,需预热处理烟气,催化剂昂贵且使用寿命短,同时存在氨泄漏、设备易腐蚀等问题。
选择性非催化还原温度区域为870~1200℃,脱硝率小于50%。
缺点是工艺设备投资大,需预热处理烟气,设备易腐蚀等问题。
二、干法烟气脱硫脱硝一体化技术干法烟气脱硫脱硝一体化技术包括四个方面:
固相吸收/再生法、气/固催化同时脱硫脱硝技术、吸收剂喷射法以及高能电子活化氧化法。
(一)固体吸附/再生法主要有碳质材料吸附法、no×so法、cuo吸附法和pahlman法。
1.碳质材料吸附法根据吸附材料的不同又可分为活性炭吸附法和活性焦吸附法两种,其脱硫脱硝原理基本相同。
活性炭吸附法整个脱硫脱硝工艺流程分两部分:
吸附塔和再生塔。
而活性焦吸附法只有一个吸附塔,塔分两层,上层脱硝,下层脱硫,活性焦在塔内上下移动,烟气横向流过塔。
该方法的主要优点有:
①具有很高的脱硫率(98%)和低温(100~200℃)条件下较高的脱硝率(80%);②处理后的烟气排放前不需加热;③不使用水,没有二次污染;④吸附剂来源广泛,不存在中毒问题,只需补充消耗掉的部分;⑤能去除湿法难去除的so2;⑥能去除废气中的hf、hcl、砷、汞等污染物,是深度处理技术;⑦具有除尘功能,出口排尘浓度小于10mg/m3;⑧可以回收副产品,如:
高纯硫磺、浓硫酸、液态so2、化学肥料等;⑨建设费用低,运转费用经济,占地面积小[2]。
日本的i.mochida提出了一种新的活性炭纤维脱硫脱硝技术。
该技术是将活性炭制成直径20μm左右的纤维状,极大地增大了吸附面积,提高了吸附和催化能力。
经过发展,现在该技术脱硫脱硝率可达90%[3]。
近年来有人将活性炭吸附和微波技术结合起来,提出了微波诱导催化还原脱硫脱硝技术。
该技术用活性炭作为氮氧化物载体,利用微波能诱导可实现脱硫脱硝率达到90%以上[4]。
2.no×so法美国的no×so公司在1982年开始进行活性氧化铝吸附法脱硫脱硝技术的研究。
该法的吸附剂是以r-氧化铝为载体,用碱或碱成分盐的溶液喷涂载体,然后将浸泡过的吸附剂加热、干燥,去除残余水分而制成。
吸附剂吸附饱和后可以再生,再生过程是将吸附饱和的吸附剂送入加热器,在温度600℃左右加热使得nox被释放,然后将nox循环送回锅炉的燃烧器中。
在燃烧器中nox的浓度达到一个稳定状态,且形成一个化学平衡。
这样就不会再生成nox而只能是n2,从而抑制nox生成。
在再生器中加入还原气体,就会产生高浓度的so2、h2s混合气体,利用克劳斯法可以进行硫磺的回收[5]。
3.cuo吸附法cuo吸附脱硫脱硝工艺法采用cuo/al2o3或cuo/sio2作吸附剂(cuo含量通常在4%-6%)进行脱硫脱硝,整个反应分两步:
1)在吸附器中:
在300℃~450℃的温度范围内,吸附剂与二氧化硫反应,生成cuso4;由于cuo和生成的cuso4对nh3还原氮氧化物有很高的催化活性,结合scr法进行脱硝。
2)在再生器中:
吸附剂吸收饱和后生成的cuso4被送到再生器中再生,再生过程一般用h2或ch4对cuso4进行还原,再生出的二氧化硫可通过claus装置进行回收制酸;还原得到的金属铜或cu2s在吸附剂处理器中用烟气或空气氧化成cuo,生成的cuo又重新用于吸收还原过程。
该工艺能达到90%以上的二氧化硫脱除率和75%~80%的氮氧化物脱除率[6、7]。
cuo吸附法反应温度要求高,需加热装置,并且吸附剂的制各成本较高。
近年来随着研究的进展,出现了将活性焦/炭(ac)与cuo结合的方法。
二者结合后可制各出活性温度适宜的催化吸收剂,克服了ac使用温度偏低和cuo/al2o3活性温度偏高的缺点。
刘守军[8]等人研究了用cuo/ac低温脱除烟气中的so2和nox,新型cuo/ac催化剂在烟气温度120~250℃下,具有较高的脱硫和脱硝活性,明显高于同温下ac和cuo/al2o3的脱除活性。
4.pahlman法美国enviroscrubtechnologies公司开发了一种新工艺—pahlman工艺[9],采用一步法干式洗涤,可脱除烟气中99%以上的硫氧化物,并可选择性地或同时除去99%的氮氧化物,排放尾气完全符合环境标准。
由于它采用无机化合物作吸收剂,而不是传统工艺中的氨,因此其副产物是可回收的硝酸盐和硫酸盐,而不是需要堆埋的污染环境的石膏副产物。
该工艺适用于以天然气或煤为燃料的发电厂,目前仍在实验阶段,未见诸工业应用。
(二)气/固催化同时脱硫脱硝技术此类工艺使用催化剂降低反应活化能,促进二氧化硫和氮氧化物的脱除,比起传统的scr工艺,具有更高的氮氧化物脱除效率。
该类工艺包括wsa-snox、desonox、snrb、parsonfgc和lurgicfb。
1.snox工艺由丹麦haldortopsor公司开发的snox(sulfurandnoxabatement)联合脱硫脱硝技术,是将so2氧化为so3后制成硫酸回收,并用选择性催化还原法scr去除nox。
此工艺可脱除95%的so2、90%的nox和几乎所有的颗粒物[10]。
2.desonox工艺desonox工艺由degussa、lentjes和lurgi联合开发,该工艺除了将烟气中的so2转化为so3后制成硫酸,以及用scr除去nox外,还能将co及未燃烧的烃类物质氧化为co2和水[11]。
此工艺脱硫脱硝效率较高,没有二次污染,技术简单,投资及运行费用较低,适用于老厂的改造。
3.snrb工艺snrb工艺是一种新型的高温烟气净化工艺,由b&w公司开发。
该工艺能同时去除二氧化硫、氮氧化物和烟尘,并且都是在一个高温的集尘室中集中处理[12]。
snrb工艺由于将三种污染物的脱除集中在一个设备上,从而降低了成本并减少了占地面积。
其缺点是由于要求的烟气温度为300℃~500℃,就需要采用特殊的耐高温陶瓷纤维编织的过滤袋,因而增加了成本。
4.parsons烟气清洁工艺parsons烟气清洁工艺已发展到中试阶段,燃煤锅炉烟气中的so2和nox的脱除效率能达到99%以上。
该工艺是在单独的还原步骤中同时将so2催化还原为h2s,nox还原为n2,剩余的氧还原为水;从氢化反应器的排气中回收h2s;从h2s富集气体中生产元素硫[13]。
5.烟气循环流化床(cfb)联合脱硫脱硝工艺循环流化床技术最初是由德国的llb(lurgilentjesbischoff)公司研究开发的一种半干法脱硫技术。
该技术在最近几年得到了快速发展,不仅技术成熟可靠,而且投资运行费用也大为降低[14],为了开发更经济、高效、可靠的联合脱硫脱硝方法,人们将循环流化床引入烟气同时脱硫脱硝技术中。
烟气循环流化床(cfb)联合脱硫脱硝技术是由lurgigmbh[15]研究开发,该方法用消石灰作为脱硫的吸收剂脱除二氧化硫,产物主要是caso4和10%的caso3;脱硝反应使用氨作为还原剂进行选择催化还原反应,催化剂是具有活性的细粉末化合物feso4·7h2o,不需要支撑载体,运行温度在385℃。
该系统在德国投入运行的结果表明,在ca/s比为1.2~1.5、nh3/nox比为0.7~1.03时,脱硫效率为97%,脱硝效率为88%[16]。
(三)吸收剂喷射同时脱硫脱硝技术将碱或尿素等干粉喷入炉膛、烟道或喷雾干式洗涤塔内,在一定条件下能同时脱除二氧化硫和氮氧化物。
脱硝率主要取决于烟气中的二氧化硫和氮氧化物的比、反应温度、吸收剂的粒度和停留时间等。
不过当系统中二氧化硫浓度低时,氮氧化物的脱除效率也低。
因此,该工艺适用于高硫煤烟气处理。
1.炉膛石灰(石)/尿素喷射工艺炉膛石灰(石)/尿素喷射同时脱硫脱硝工艺由俄罗斯门捷列夫化学工艺学院等单位联合开发。
该工艺将炉膛喷钙和选择非催化还原(sncr)结合起来,实现同时脱除烟气中的二氧化硫和氮氧化物。
喷射浆液由尿素溶液和各种钙基吸收剂组成,总含固量为30%,ph值为5~9,与干ca(oh)2吸收剂喷射方法相比,浆液喷射增强了so2的脱除,这可能是由于吸收剂磨得更细、更具活性[17]。
gullett等人采用14.7kw天然气燃烧装置进行了大量的试验研究[18]。
该工艺由于烟气处理量太小,不能满足工业应用的要求,因而还有待改进。
2.整体干式so2/nox排放控制工艺整体干式so2/nox排放控制工艺采用babcock&wilcox公司的低noxdrb-xcl下置式燃烧器,这些燃烧器通过在缺氧环境下喷入部分煤和空气来抑制氮氧化物的生成。
过剩空气的引入是为了完成燃烧过程,以及进一步除去氮氧化物。
低氮氧化物燃烧器预计可减少50%的氮氧化物排放,而且在通入过剩空气后可减少70%以上的nox排放[19]。
无论是整体联用干式so2/nox排放控制系统,还是单个技术,都可应用于电厂或工业锅炉上,主要适用于较老的中小型机组。
(四)高能电子活化氧化法目前主要有电子束照射法和脉冲电晕等离子体法。
1.电子束照射法利用阴极发射并经电场加速形成高能电子束,这些电子束辐照烟气时产生自由基,再和sox和nox反应生成硫酸和硝酸,在通入氨气(nh3)的情况下,产生(nh4)2so4和nh4no3氨盐等副产品。
日木荏原公司经过20多年的研究开发,己从小试逐步走向工业化。
脱硫率90%以上,脱硝率80%以上。
但耗电量大(约占厂用电的2%),运行费用高[20]。
2.脉冲电晕等离子体法(ppcp)masuda等人1986年发现电晕放电可以同时脱除二氧化硫和氮氧化物,该方法由于具有设备简单、操作简便,显著的脱硫脱硝和除尘效果以及副产物可作为肥料回收利用等优点而成为国际上脱硫脱硝的研究前沿[21-23]。
脉冲电晕等离子体技术和电子束法均属于等离子体法.脉冲电晕与传统的液相(氢氧化钙或碳酸氢铵)吸收技术相结合,提高了烟气二氧化硫和氮氧化物的脱除效率,实现脱硫、脱硝的一体化[24-25]。
脉冲电晕放电脱硫脱硝有着突出的优点,在节能方面有很大的潜力,对电站锅炉的安全运行也没有影响[26]。
三、湿法烟气脱硫脱硝一体化技术湿法烟气同时脱硫脱硝工艺通常在气/液段将no氧化成no2,或者通过加入添加剂来提高no的溶解度。
湿式同时脱硫脱硝的方法目前大多处于研究阶段,包括氧化法和湿式络合法。
(一)氧化法氯酸氧化工艺(又称丁tri-nox-noxsorb工艺)是采用湿式洗涤系统,在一套设备中同时脱除烟气中的二氧化硫和氮氧化物[27]。
tri-nox-noxsorb工艺采用氧化吸收塔和碱式吸收塔两段工艺,在脱除二氧化硫和氮氧化物的同时脱除有毒微量金属元素,如as、be、cd、cr、pb、hg和se[28]。
isabelle等[29]研究了在酸性条件下利用双氧水将nox和so2氧化成硝酸和硫酸的工艺。
黄磷氧化法是将no氧化为no2,与液态的碱性吸收浆液反应生成硫酸盐和硝酸盐,对二氧化硫和氮氧化物的去除率达到95%以上,但黄磷具有易燃性、不稳定性和一定的毒性,需用预处理的方法解决这些问题[30]。
3.2湿式络合吸收工艺湿式络合吸收工艺一般采用铁或钴作催化剂。
在水溶液中加入能络合no的络合剂后,使之结合成络合物。
与络合剂结合的no可与溶液中的so32-/hso3-发生反应,形成一系列n-s化合物,并使络合剂再生[31]。
该工艺需通过从吸收液中去除连二硫酸盐、硫酸盐和n-s化合物以及三价铁螯合物还原成亚铁螯合物而使吸收液再生[32]。
湿式络合吸收法工艺可以同时脱硫脱硝,但目前仍处于试验阶段。
影响其工业应用的主要障碍是,反应过程中螯合物的损失和金属螯合物再生困难、利用率低,因而存在运行费用高等问题。
四、结论与建议脱硫脱硝一体化工艺已经成为各国控制烟气污染的研发热点,目前大多数脱硫脱硝一体化工艺仅停留在研究阶段,尽管已经有少量示范工程应用,但由于运行费用较高制约了其大规模推广应用。
开发适合我国国情,投资少、运行费用低、效率高、副产品资源化的脱硫脱硝一体化技术成为未来发展的重点。
[参考文献][1]王旭伟,鄢晓忠,陈彦菲,等.国内外电厂燃煤锅炉烟气同时脱硫脱硝技术的研究进展[j].电站系统工程,2007,23(4):
5-7.[2]陶宝库,王德荣,宋刚,等.固体吸附/再生法同时脱硫脱硝的技术[j].辽宁城乡环境科技,1998,6:
8-12.[3]范浩杰,朱敬,刘金生,等.活性炭纤维脱硫、脱硝的研究进展[j].动力工程,2005,25(5):
724-727.[4]马双忱,赵毅,马宵颖,等.活性炭床加微波辐射脱硫脱硝的研究[j].热能动力工程,2006,7(4):
338-341.[5]jlhaslbeck,lgneal,wtma.developmentstatusofthevoxso-combinednox-/so2fluegastreatmentprocess[j].integratedenvironmentalcontrol,1998(3):
2-4.[6]kyungseunyoo,sangmunjeong,sangdonekim,etal.regenerationofsulfatedaluminasupportincuo/al2o3sorbentbyhydrogen[j].eng.chem.res.,1996,35(5):
1543-1549.[7]mashuang-chen,jinyi-jing,jinxin,etal.influencesofco-existingcomponentsinfluegasonsimultaneousdesulfurizationanddenitrificationusingmicrowaveirradiationoveractivatedcarbon[j].jfuelchemtechnol,2011,39(6),460-464.[8]刘守军,刘振宇,朱珍平,等.cuo/ac脱除烟气中so2机理的初步研究[j].煤炭转化,2000,23
(2):
67-71.[9]pahlman.烟气脱硫脱硝工艺[j].硫酸工业,2002,4.[10]schoubye,ptopse.snoxprocessremovesnoxandsoxassulfuricacid.proc.util.highsulfurcoal[j].procintconf2nd,1989,875-880.[11]norbertohlms.desonoxfluegaspurificationprocessdesonoxprocessforfluegascleaning[j].catalysistoday,1993,16
(2):
247-261.[12]saleema.designandoperationofsingletrainspraytowerfgdsystem[a]paperpresentedatso2controlsymposium[c].washingtondc,usa,1991,3-6.[13]kwongkv,remeissner,iii,midcchong.recentdevelopmentsintheparsonsfgcprocessforsimultaneousremovalofsoxandnox[j].so2controlsymposium,1991
(2):
3-6.[14]rgraf,jdriley.dry/semi-dryfluegasdesulfurizationusingthelurgicirculatingfluidbedabsorptionprocess[m].1995.[15]单志峰,黄友明.国外烟气同步脱硫脱硝技术现状[j].冶金环境保护,1999,4:
40-45.[16]钟秦.燃煤烟气脱硫脱硝技术及工程实例[m].北京:
化学工业出版社,2002:
331-335.[17]徐维正.用尿素净化烟道气的新工艺[j].化工科技动态,1993,3(4):
43-47.[18]wdepriestetal.uspbrep,1989,(pb-89-220537):
987-9107.[19]lesliel.slossetal.nitrogenoxidescontroltechnologyfactbook[m],printedintheunitedstatespublishedintheunitedstatesofamericabynoyesdatacorporation,1993.[20]宋增林,王丽萍,程璞.火电厂锅炉烟气同时脱硫脱硝技术进展[j].热力发电,2005,2:
6-9.[21]giorgiodinelli,luigicivitano,massimorea.industrialexperimentsonpulsecoronasimultaneousremovalofnoxandso2fromfluegas[j].ieeetransactionsonindustryapplications,1990,26(3):
535-541.[22]takaonamihira,shunsuketsukamoto,douyanwang,etal.influenceofgasflowrateandreactorlengthonnoremovalusingpulsedpower[j].ieeetransactionsonindustryapplications,2001,29(4):
592-598.[23]limindong,shouguosheng,lutaoliu,etal.removalofnoxandso2inplasmareactorwithwaterfilm[j].in:
xxthinternationalsymposiumondischargesandelectricalinsulationinvacuum-tours.2002,423-426.[24]huangliwei,dangyongxia.removalofso2andnoxbypulsedcoronacombinedwithinsituca(oh)2absorption[j].chinesejournalofchemicalengineering,2011,19(3):
518-522.[25]zaishanwei,zhehanglin,hejingyingniu,etal.simultaneousdesulfurizationanddenitrificationbymicrowavereactorwithammoniumbicarbonateandzeolite[j].journalofhazardousmaterials,2009,162:
837-841.[26]toshiakiyamamoto,masaakiokubo,takaonagaoka,kunihirohayakawa.simultaneousremovalofnox,soxandco2atelevatedtemperatureusingaplasma-chemicalhybridprocess[j].ieeetransactionsonindustryapplications,2002,38(5):
1168-1173.[27]kaezur,jerryj.oxidationchemistryofchloricacidinnox/soxandairtoxicmetalremovalfromgasstreams[j].environmentalprogress,1996,15(4):
245-354.[28]chientw,chuh,hsuehht.kineticstudyonabsorptionofso2andnoxwithacidicnaclo2solutionsusingthesprayingcolumn[j].journalofenvironmentalengineering,2003,129(11):
967-974.[29]changsg,leegc.lblphosnoxprocessforcombinedremovalofso2andnoxfromfluegas[j].environmentalprogress,1992,11
(1):
66-73.[30]isabelleliémans,brunoalban,jean-pierretranier,etal.soxandnoxabsorptionbasedremovalintoacidicconditionsforthefluegastreatmentinoxy-fuelcombustion[j].energyprocedia,2011,4:
2847-2854.[31]王慧,李先国,韩欣欣.金属络合剂在烟气同时脱硫脱硝中的应用[j].化工环保,2007,27(5):
421-425.[32]周春琼,邓先和.钴络合物体系同时脱硫脱硝实验研究[j].广西师范大学学报(自然科学版),2007,25(3):
79-52.目录
第一章总论1
1.1项目背景1
1.1.1项目名称及承办单位1
1.1.2承办单位1
1.1.3项目建设地点1
1.1.4可行性研究报告编制单位1
1.2报告编制依据和研究范围1
1.2.1报告编制依据1
1.2.2研究范围2
1.3承办单位概况2
1.4项目提出背景及必要性3
1.4.1项目提出的背景3
1.4.2项目建设的必要性4
1.5项目概况5
1.5.1建设地点5
1.5.2建设规模与产品方案5
1.5.3项目投资与效益概况5
1.6主要技术经济指标6
第二章市场分析及预测8
2.1绿色农产品市场分析及预测8
2.1.1生产现状8
2.1.2市场前景分析