180万吨甲醇可研报告.docx
《180万吨甲醇可研报告.docx》由会员分享,可在线阅读,更多相关《180万吨甲醇可研报告.docx(69页珍藏版)》请在冰豆网上搜索。
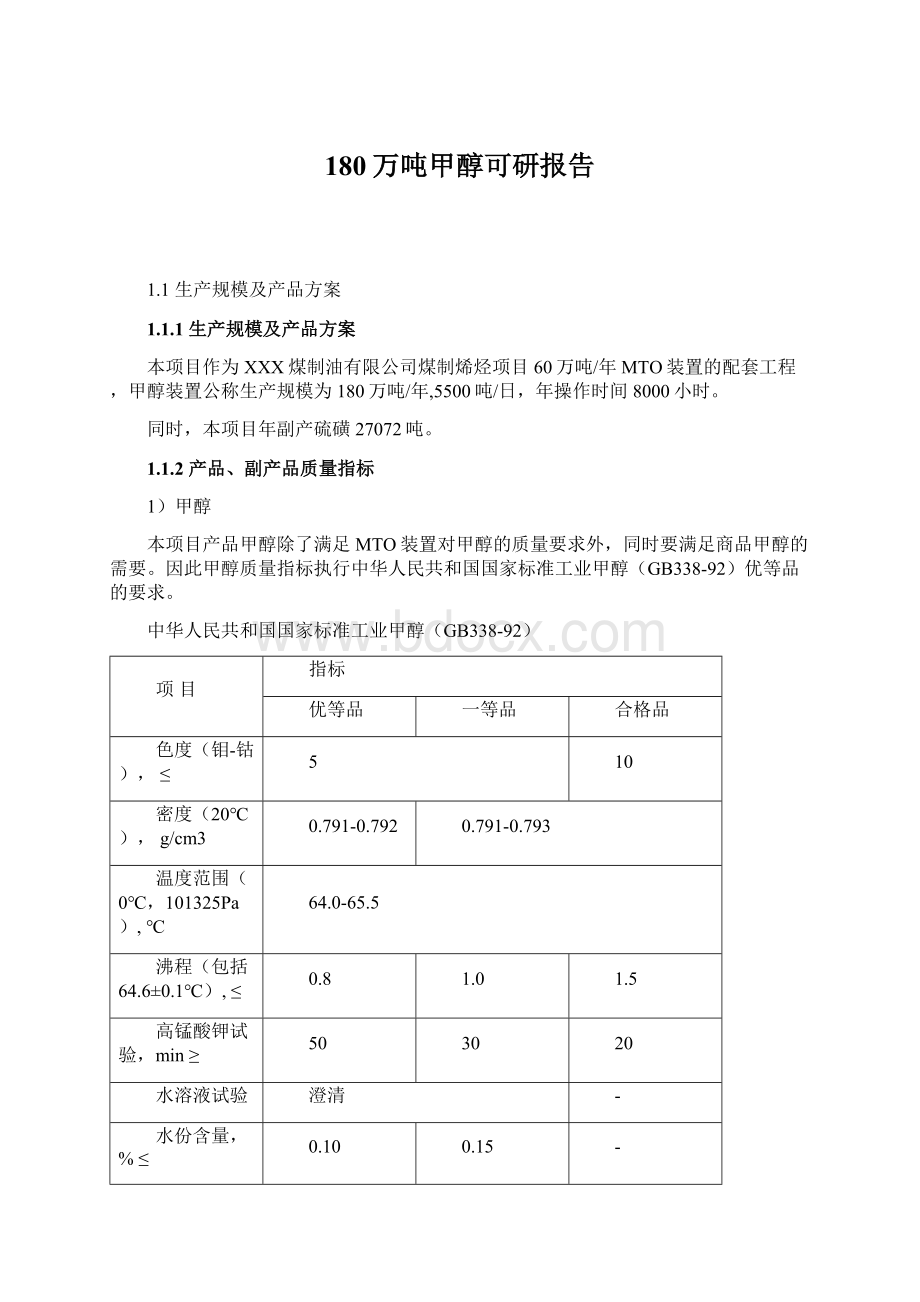
180万吨甲醇可研报告
1.1生产规模及产品方案
1.1.1生产规模及产品方案
本项目作为XXX煤制油有限公司煤制烯烃项目60万吨/年MTO装置的配套工程,甲醇装置公称生产规模为180万吨/年,5500吨/日,年操作时间8000小时。
同时,本项目年副产硫磺27072吨。
1.1.2产品、副产品质量指标
1)甲醇
本项目产品甲醇除了满足MTO装置对甲醇的质量要求外,同时要满足商品甲醇的需要。
因此甲醇质量指标执行中华人民共和国国家标准工业甲醇(GB338-92)优等品的要求。
中华人民共和国国家标准工业甲醇(GB338-92)
项目
指标
优等品
一等品
合格品
色度(钼-钴),≤
5
10
密度(20℃),g/cm3
0.791-0.792
0.791-0.793
温度范围(0℃,101325Pa),℃
64.0-65.5
沸程(包括64.6±0.1℃),≤
0.8
1.0
1.5
高锰酸钾试验,min≥
50
30
20
水溶液试验
澄清
-
水份含量,%≤
0.10
0.15
-
酸度(以HCOOH计),%≤
0.0015
0.0030
0.0050
碱度(以NH3计),%≤
0.0002
0.0008
0.0015
羰基化合物(以CH2O计),≤
0.002
0.005
0.010
蒸发残渣含量,%≤
0.001
0.003
0.005
2)副产品硫磺
硫磺产品符合中华人民共和国国家标准(GB2449-92)优等品指标。
项目
指标
优等品
一等品
合格品
硫,%≥
99.9
99.5
99.0
酸度(以H2SO4计),%≤
0.003
0.005
0.02
水份,%≤
0.10
0.50
1.00
灰份,%≤
0.03
0.10
0.20
砷,%≤
0.0001
0.01
0.05
粒度
片状
片状
片状
1.2工艺技术选择
1.2.1原料路线确定
甲醇是由一氧化碳与氢在催化剂存在的情况下进行化学反应而制得。
煤、焦炭、天然气、炼厂气、石脑油(轻油)、渣油(重油)、焦炉气和乙炔尾气等均可用来制造一氧化碳和氢(合成气),作为合成甲醇的原料。
在甲醇生产装置中,合成气的制备,在装置总投资中占绝大部分(约为60%),而甲醇的合成、粗甲醇的精馏以及公用工程等部分的投资所占比例较少,所以,甲醇生产原料路线的选择,主要是对合成气制备所用原料以及工艺路线的选择。
甲醇生产装置各工序的投资比例见下表:
甲醇生产装置各工序投资比例表
序号
项目
占总投资的比例
1
合成气制备(包括气化、净化、冷冻)
60%
2
甲醇合成
10%
3
甲醇精馏
10%
4
公用工程等
20%
选用生产甲醇合成气的原料,可以从原料储量、现有生产能力、原料价格、成本、投资费用与技术水平等进行综合考虑。
XXX集团万利煤矿地处鄂尔多斯市,矿区有丰富的煤炭资源,从储量和目前的生产能力上看,完全可满足合成甲醇所需合成气原料的需要。
以煤或天然气为原料制合成气的生产工艺都比较成熟,国内外都有大型工业化装置在运转。
国外大型甲醇装置大多采用以天然气为原料的生产路线,主要原因除了一次性投资较低外,也与国外的天然气价格低有关。
比如沙特阿拉伯1998年的天然气价格为0.15元/Nm3,目前价格为0.279元/Nm3。
俄罗斯的天然气价格在0.20元/Nm3左右。
因此中东地区及俄罗斯以天然气为原料的大型甲醇生产装置甲醇成本较低,约在100~120美元之间。
近年来,美国的天然气价格上涨幅度较大,由0.5元/Nm3涨到0.7元/Nm3,2001~2002年已先后关闭340万吨甲醇生产能力。
一般认为,天然气价格高于0.7元/Nm3,则甲醇成本大于1100元/吨,已无竞争能力。
与国外相比,我国以天然气为原料的甲醇厂由于规模小(目前最大能力为20万吨/年)、能耗高(一般为1100~1260Nm3/t,最高达1770Nm3/t甲醇),其成本一般为1300~1400元/吨。
2002年我国进口179.96万吨甲醇,到岸价全年平均为154.88美元/吨(折人民币1285.5元),我国以天然气为原料的甲醇厂生产的甲醇在价格上无法与国外同类产品竞争。
然而,以煤为原料的大型甲醇生产装置,则产品成本较低,且有成熟技术,可以与国外厂家相竞争。
本项目推荐以煤为原料生产甲醇的技术路线。
1.2.2工艺技术方案比较与选择
1)气化工艺技术
a)国外气化工艺技术概况
以煤为原料的气化方法主要有固定床和流化床、气流床等。
固定床气化技术
固定床气化技术在我国运用较广,较为先进的有鲁奇(Lurgi)气化技术。
此技术经过英国煤气公司和鲁奇公司联合攻关,开发一种新炉型-BGL炉,变干粉排渣为熔融排渣,气化效率和气体成分有了很大改进,污染问题也有所改善。
现有一台工业示范炉在德国运行,用于处理城市垃圾,所用原料为各种城市垃圾、废塑料和烟煤。
但因气化温度变化不大,生成气中甲烷及氮气含量大,不宜做合成气;但其热值较高,用于做城市煤气较好。
流化床气化技术
流化床气化技术主要有德国温克勒(Winkler)流化床粉煤气化技术。
该技术压力较低,建有生产燃料气的装置,目前没有生产合成气的装置。
气流床气化技术
气流床气化技术有美国德士古气化(Texaco)技术和荷兰壳牌谢尔(shell)粉煤加压气化技术。
b)国内气化工艺技术概况
固定床气化
固定层间歇气化技术,该技术投资低,技术成熟,目前我国小氮肥、小甲醇厂90%以上采用该工艺生产。
该技术气化效率低,单炉产气量少,常压间歇气化,吹风过程中放空气对环境污染严重,每吨合成氨的吹风放空气量达2800~3100立方米。
该技术在国外已被淘汰。
国内固定床气化还有富氧连续气化技术,虽然该技术连续气化无吹风气排放,污染较少,但只能采用焦炭或无烟煤作原料,原料价格高,且生成气中氮气含量高,不适合作合成甲醇的原料气。
流化床气化
国内流化床气化主要有中科院山西煤化学研究所开发的灰熔聚流化床粉煤气化技术,该技术可用多种煤质作原料,如烟煤、焦炭、焦粉等,使用粉煤在1100℃下气化,固体排渣,无废气排放。
该技术工业示范装置已于2001年在陕西城固氮肥厂建成,小时耗煤量4 .2吨。
其煤种适应性广,操作温度约为1000℃,反应压力为0.03MPa(G)。
气化炉是一个单段流化床,结构简单,可在流化床内一次实现煤的破粘、脱挥发份、气化、灰团聚及分离、焦油及酚类的裂解。
带出细粉经除尘系统捕集后返回气化炉,再次参加反应,有利于碳利用率的进一步提高。
产品气中不含焦油,含酚量低。
碳转化率为90%。
主要的缺点是合成气中(CO+H2)为68~72%,有效气体成分较低,其次是气化压力低、单炉产气量小。
恩德粉煤气化
恩德粉煤气化技术,在朝鲜有30多年的运行经验,适用于灰分不大于40%的褐煤、长焰煤、不粘或弱粘结的煤粉(0~10mm)。
气化剂采用蒸汽和富氧,富氧分为两段加入气化炉,在常压下进行气化反应,反应温度为1000~1100℃,固态排渣,无废气排放。
气化炉无炉筚,空筒气化,操作可靠,气化炉运转率可达92%。
单炉产气量有10000Nm3/h,20000Nm3/h,40000Nm3/h等。
合成气(CO+H2)为62~65%,CO2为27~28%,其它为惰性组分。
由于气化剂为富氧,故合成气中氮气含量高,故此合成气适用于作为合成氨原料气。
主要的缺点也是有效气体成分较低、且含氮高,气化压力低、单炉产气量小。
气流床气化
我国煤气化技术科研人员经过多年努力研究,开发出了具有中国知识产权的煤气化技术,即华东理工大学会同鲁南化肥厂等单位合作开发的水煤浆四喷嘴撞击流气化技术,该技术氧耗、煤耗比德士古气化技术低,碳转化率可达98%,有效气体成分(CO+H2)83~85%,这些指标均比德士古气化技术高。
采用该技术建立的日处理煤量20吨的工业性试验装置已运转400小时以上,并经过72小时考核,取得了国家专利,经过科技部组织的评审与验收。
德州恒升公司大氮肥国产化工程及兖矿集团年产24万吨甲醇项目均采用了该技术,现正在设计、建设中。
由于该技术中试试验时间较短,大型装置未投产验证,有一定的风险。
气化炉烧嘴较多,停车检修或更换烧嘴时影响面较大,由于采用四喷嘴,需要配多台高压煤浆泵及相应管线和仪表控制系统,加之炉体加长,气化流程中增加了分离器等,投资与采用德士古水煤浆气化技术相比(计入德士古专利费后)略低。
以日处理750吨煤的气化炉进行比较,初步估算投资费用差别如下:
德士古与四喷嘴炉投资比较
气化技术
德士古水煤浆气化
水煤浆四喷嘴撞击流气化
德士古炉-四喷嘴炉
气化炉设备费(万元)
1台
1台
-200
煤浆泵设备费
1台
2台
-200
自控仪表材料费(万元)
1套
4套
-500
其他工程费(万元)
-410
软件费(万元)
1660
200
1460
合计(万元)
150
从上表可看出,水煤浆四喷嘴撞击流气化炉和典型的德士古水煤浆气化炉相比,硬件投资增加,但软件投资可节省,两者相抵,总投资相差不多,采用国内有自主知识产权的四喷嘴撞击流气化炉稍微低一点。
但鉴于该炉型尚无工业运行的经验,加之事故和停车的几率增加,运行的可靠性较差,故本项目暂不推荐。
原化工部临潼化肥研究所(现西北化工研究院)早在60年代末就已开展水煤浆纯氧气化的研究,70年代初建立日处理50吨的气化装置。
从水煤浆制备、纯氧气化、灰水处理等试验中取得工艺流程的优化,最终工艺条件的选择、设备材料的选择、自动控制,软件开发等一系列工程数据。
本世纪初该院又开发了焦煤水加添加剂的混合煤浆气化技术,已成功地应用于油气化装置的改造,建有工业化装置,该技术已申请国家专利并获得批准,专利号00113911.8。
为配合水煤浆气化的研究试验工作,洛阳材料研究所研究制成了水煤浆气化炉的耐火砖,原化工部化工机械研究所开发了二流道、三流道的烧嘴,重庆热工仪表研究所开发了适于水煤浆气化的测温度计等。
这一系列科研成果得到了化工部科技司、国家科委的大力支持和技术鉴定,为今后我国水煤浆气化工程应用奠定了基础,也为工程设计提供了基础数裾。
c)气化技术的选择
目前大型煤气化技术较为先进的有Texaco水煤浆气化,Shell粉煤加压气化,Lurgi固定床加压气化。
国外大型气化技术比较表
项目
Texaco
Shell
Lurgi(传统)
气化压力
3.0~6.5
2.0~4.0
3.0
气化温度℃
1300~1400
1400~1600
850
单炉最大能力
吨煤/天
500~2000
2000
600
气化炉型式
热壁式、单喷嘴
冷壁炉、四喷嘴
热壁炉
进煤方式
水煤浆浓度
>60%泵送
煤粉用氮气输送
粒度90%<90μm
碎煤干法加料
热回收方式
激冷、废锅
废锅
废锅
排渣
液态排渣
液态排渣
固态排渣
碳转化率%
96—98
>99
90
有效成份(CO+H2)
较高>80%
高>90%
68%
净化气中惰性气含量
<0.5%
5%
10%(N2+CH4+Ar)
吨甲醇耗煤量(干,弛放气氢回收时)
1.31
1.27
1.5
氧气用量
高(比Shell炉高10%)
较低
低
工业化装置数
7
1
多
在中国已投产/在建的工业装置
4/7
0/7
4/0
环境影响
友好
友好
有污染治理问题
投资(含空分)
较低
高(比Texaco约高15%)
较低
国产化率
高