企业精益经营心得体会六篇.docx
《企业精益经营心得体会六篇.docx》由会员分享,可在线阅读,更多相关《企业精益经营心得体会六篇.docx(8页珍藏版)》请在冰豆网上搜索。
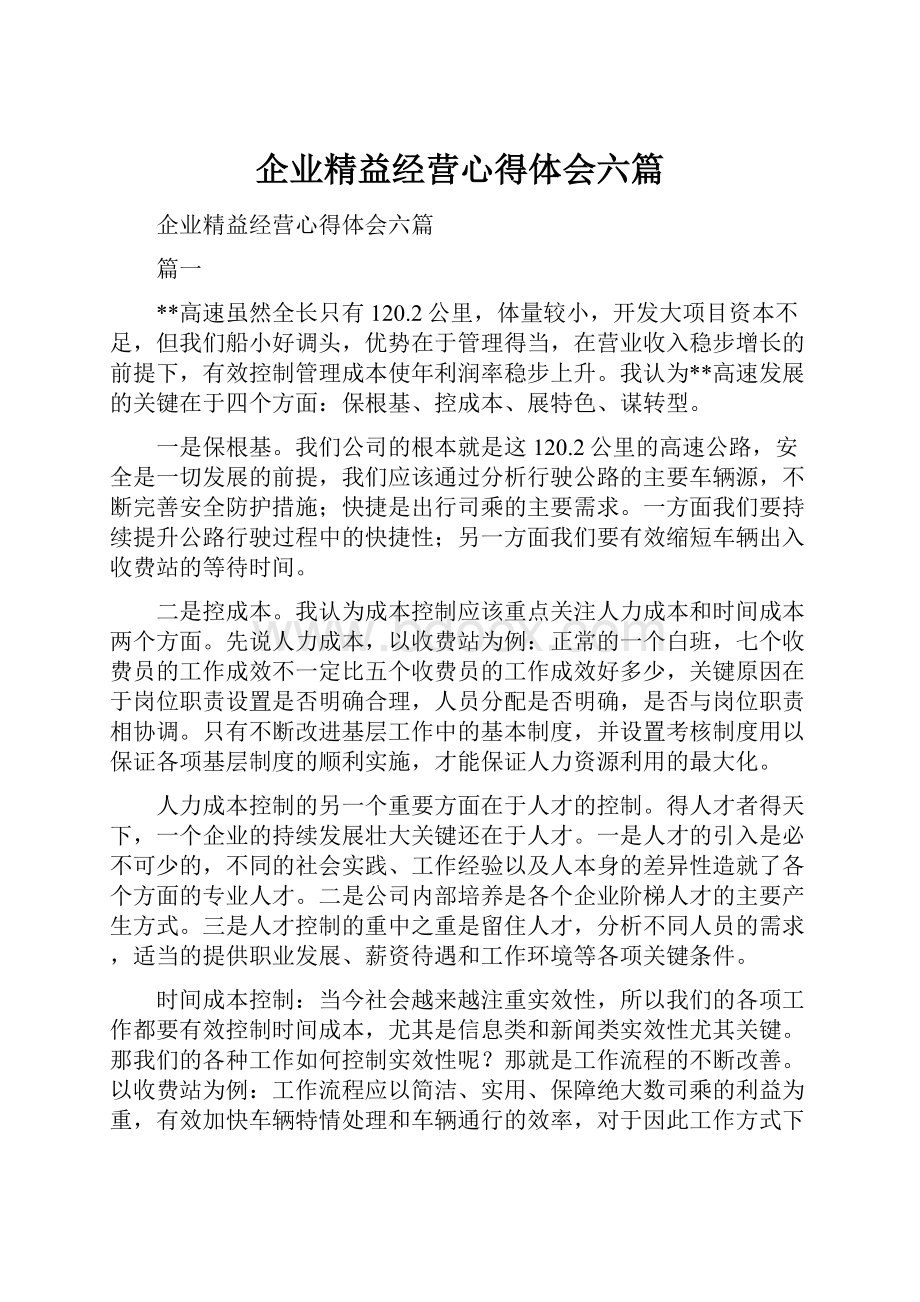
企业精益经营心得体会六篇
企业精益经营心得体会六篇
篇一
**高速虽然全长只有120.2公里,体量较小,开发大项目资本不足,但我们船小好调头,优势在于管理得当,在营业收入稳步增长的前提下,有效控制管理成本使年利润率稳步上升。
我认为**高速发展的关键在于四个方面:
保根基、控成本、展特色、谋转型。
一是保根基。
我们公司的根本就是这120.2公里的高速公路,安全是一切发展的前提,我们应该通过分析行驶公路的主要车辆源,不断完善安全防护措施;快捷是出行司乘的主要需求。
一方面我们要持续提升公路行驶过程中的快捷性;另一方面我们要有效缩短车辆出入收费站的等待时间。
二是控成本。
我认为成本控制应该重点关注人力成本和时间成本两个方面。
先说人力成本,以收费站为例:
正常的一个白班,七个收费员的工作成效不一定比五个收费员的工作成效好多少,关键原因在于岗位职责设置是否明确合理,人员分配是否明确,是否与岗位职责相协调。
只有不断改进基层工作中的基本制度,并设置考核制度用以保证各项基层制度的顺利实施,才能保证人力资源利用的最大化。
人力成本控制的另一个重要方面在于人才的控制。
得人才者得天下,一个企业的持续发展壮大关键还在于人才。
一是人才的引入是必不可少的,不同的社会实践、工作经验以及人本身的差异性造就了各个方面的专业人才。
二是公司内部培养是各个企业阶梯人才的主要产生方式。
三是人才控制的重中之重是留住人才,分析不同人员的需求,适当的提供职业发展、薪资待遇和工作环境等各项关键条件。
时间成本控制:
当今社会越来越注重实效性,所以我们的各项工作都要有效控制时间成本,尤其是信息类和新闻类实效性尤其关键。
那我们的各种工作如何控制实效性呢?
那就是工作流程的不断改善。
以收费站为例:
工作流程应以简洁、实用、保障绝大数司乘的利益为重,有效加快车辆特情处理和车辆通行的效率,对于因此工作方式下产生的个别逃费嫌疑车辆以后期服务管控科处理作为有效控制和补充。
三是展特色和促转型。
2018年的鼓浪屿之行给我的触动很大,鼓浪屿的面积只有1.91平方公里,,自然资源条件也只是一般,但他利用现有资源加以人工改造,给人营造出一种幽静、舒适和原始相结合的味道。
尤其是鼓浪屿的夜晚,安静的小巷、间隔不远的黄色灯光以及温柔海风中混入的勾人的海鲜味道,温暖舒适让人流连忘返。
鼓浪屿的另一个特点就是景点小而精致。
既有日光岩那种自然景观,又有玫瑰园这类几十平方米的人造公园还有众多的占地只有两层别墅大小的蜡像馆、博物馆等。
我认为鼓浪屿的这种利用有限资源加以人工改造,以细腻婉约派为主的做法值得借鉴。
篇二
**公司正式推行精益经营已有一段时间,通过学习以及在工作中的初步实践,逐步使我明确了精益的目的和宗旨是什么,精益的思维是怎样的,同时也深入学习了一些管理工具。
接下来就我本人对精益管理的一些粗浅认知与大家进行交流:
首先,精益管理是一种系统性的管理思维,有目的、有宗旨、有原则、有工具。
精益的目的是消除浪费、降低成本,这是具备精益思维的前提和基础,是所有工作的着眼点和落脚点,不论做什么工作,要始终清晰的知道并贯彻这一目的,才不会走偏。
宗旨,我理解的有两点,一是把握“成本、速度、质量”的宗旨,所有工作都要从这三方面的有机结合和协调统一方面入手,既不能为了追求成本的降低而忽视质量,也不能只关注质量而不计成本的投入。
应该找到合适的结合点,使三者统一协调,做到“刚刚好”。
二是时刻聚焦目标,这是我从《精益的一天》中获得的感悟,Williams小学是一所快速发展的学校,在6年的时间里扩建两次,但是她仍能够很好的完成教学目标,同时恰当的应付了各种突发事件。
Williams小学的目标是建立一个学习和教育的环境,在这一目标的引领下,学校所有教职员工的工作都是围绕如何打造良好有序的学习和教育环境而开展,没有各种繁杂的事务干扰,教师们聚焦目标,工作简单而有效。
学校的设施设置想必也是一样,没有大而全的改造,也没有高大上的投入,所有设置都是必须且必要,没有资源的闲置和空间的浪费。
其次,既然是思维方式,那么植入人心最重要。
让精益成为我们的工作习惯,不需提醒,就像呼吸一样,成为一种本能的反应是我们追求的目标。
那么如何才能使精益有效的落地,让大家自觉自愿的接受并践行精益理念,我认为可通过三个层面的共同努力来逐步打造。
一是公司的顶层设计,设置公司层面的目标,这个目标与公司的兴衰和发展相关,与每一名员工的职业命运息息相关,这样就可以把所有员工的利益与公司的利益高度统一在一起,员工与公司有了共同目标,就有了协作的基础。
例如,可以设置公司的利润与员工收入挂钩的目标等。
二是通过必要的形式推动员工对精益的运用。
如设立“精益日”,规定每月的哪一天为精益管理日,这一天所有人放下手头所有其他工作,专注精益。
一则可以让员工从繁杂的日常事务中解脱出来,可以有机会用精益的眼光专心的审视本职工作,二也便于引起员工的足够重视并逐渐形成习惯。
精益日推行初期,可以由精益小组组织或协助开展,利用沙龙、头脑风暴会或者专项指导、重点指导等方式,对公司、各部门间以及某些重点部门内存在的问题进行讨论,重点解决。
通过不断的引导和帮助,逐步加深大家对精益的理解和认可,逐渐形成自发的习惯。
三是各单位要有意识的运用,各单位可通过问题入手,运用改善创新案例提报的方式,对本单位各岗位存在的问题进行梳理改善。
部门内部在开展的时候,可以运用及时叫停的方法,对于工作中发现的问题要及时叫停,立即展开讨论,共同找到最优解决方案。
对于现地现物的运用,非业务部门可通过参与或亲历员工的具体工作来发现问题,从而帮助员工优化流程,建立简洁高效的工作环境。
最后,精益管理不是一蹴而就的,也不是独立完成的,需要我们用持续发展、协作共赢的态度对待,用接纳的心态去推行,相信通过我们共同的努力,最终精益管理会成为我们的思维习惯。
篇三
近期把精益经营的理念运用到工作中,对目视化管理和三现主义又有了一些体会。
运用视觉管理使问题无处隐藏,是最基本的第一条原则。
在日常工作中,目视化管理主要运用在办公管理一块,最基本的人员去向牌、计划工作表等,往深里挖掘,各项工作都能通过目视化管理,通过简单的视觉指示,可以一眼看到问题所在,是不是在有异常。
结合到机电维护工作中,可以把设备的状态标准、维护要求与资产卡片结合起来,随时关注。
把隐藏的问题都表露出来,才不至于措手不及,有问题不可怕,可怕的是看不到问题。
亲临现场查看以彻底解决问题,是我们工作中经常用到的原则。
亲自到现场、亲自接触实物、亲自了解现实情况,这就是三现主义,要求我们不要期望坐在办公室里,面对着计算机解决现场发生的问题,而一定要到现场去,了解现物和现实,真正有效地帮助现场解决问题。
机电工作中离不开现地现物,小到故障维修,大到专项工程,只看图纸、说明书也能解决问题,但是效果相差甚远,只有真正的去深入现场,拿到第一手的资料,才能了解事情的真实情况,才能把偏差做到最小。
把精益的理念作为一种常态放在日常工作里,形成习惯才能有收获。
篇四
“精益经营”对我来说是个全新的概念,通过一次次“精益”学习、培训、讨论,切实感受到了公司对推行精益管理的决心和重视。
我们要把学习作为一种习惯、一种追求,用学习来补充精益能量,用学中干、干中学来推动精益工作持续有效开展。
第一步,转变观念。
精益是一种思维模式,是持续改善,不断学习的过程。
一个人从事一项工作,如果时间太久,常常会茫茫然而不知所以然,丧失了激情和斗志,那么就需要一场深刻的思想革命。
不是去革别人的命,而是要首先革自己的命,与旧我决裂,拥抱全新的自己。
它需要冒险精神和持之以恒的毅力,可以说精益是一场改善与坚持地长征。
第二步,立即行动。
将改善融入到日常的工作流程中去,这才是最终的目的。
没有行动,一切都是空谈。
这个行动,需要公司所有人的积极参与,形成自上而下、自下而上、平行单位三位一体立体式的改善态势。
管理人员必须率先垂范、走进现场,迅速行动,要亲自去现场了解情况,并与员工一起共同分析,寻找解决之道。
否则,会因为我们的武断和瞎指挥而推行中途夭折。
也有人认为精益管理的实施是精益部门的事情,与其它的部门无关。
事实上,如果我们其它部门不能协调一致的话,就算精益部门水平再高,那也只是“昙花一现”,无法持续发挥精益的效能。
第三步,持续改善。
精益的一切改善的前提是以客户为中心。
天下难事,必作于易;天下大事,必作于细。
持续改善,要从提高自己的责任心开始,从自己身边的小事做起,多用心思少花钱,多用心思少用人,多用心思少用物;要从源头上找问题,不断问为什么,寻求根源再解决。
必须掌握好基本功,建立标准是持续改善的基础,标准也要不断调整修改,新的代替旧的,才能到达到更好的效果。
改善是一项只有起点没有终点,并持续提高、循序渐进的进程工作,只要有耐心、能坚持就能取得成效的工作,所以要养成持之以恒的习惯。
总之,任何不能为客户增加价值的工作都是一种浪费。
精益的最终目的就是通过各种精益的工具和方法来改善存在于现场的形形色色的浪费。
我们不必要争“虚荣”,而要真正让顾客感动;要全员有“看得见的”努力,而不是僵硬的“可视化”管理;那么效益只是随之而来的一个结果罢了。
篇五
精益管理像一股新鲜的血液注入到我们质监系统,像一缕春风吹进每一位员工的心里。
经过一段对精益管理的学习,让我受益非浅。
精益管理把先进的监管理念和管理方法传授给我们,使我们无论在单位还是在日常生活中都能发挥它的作用。
精益管理是指整理、整顿、清扫、清洁、素养,因其日语的拼音均以“s”开头,因此简称为“5s”。
整理是要区分“要”与“不要”的东西,对“不要”的东西进行处理,来腾出空间,提高生产效率。
整顿是要把东西依规定定位、定量摆放整齐,明确标识,以排除寻找的浪费。
清扫是指工作场所内的脏污,设备异常马上修理,并防止污染的发生,使不足、缺点明显化,是品质的基础。
清洁是将上面实施制度化、规范化,并维持效果。
素养是要人人依规定行事,养成好习惯,以提升“人的品质”,养成对任何工作都持认真态度的人。
另外还有非常重要的一点就是“安全”,安全是指单位及每一位员工的安全,在这里是着重强调安全的重要性。
在日常的工作中,突出的问题是要查找和使用以前的某些文件资料、执法文书,表格,相关信息,案卷,办公用品等,往往翻箱倒柜,东找西找,大部分时间浪费了,工作效率很难提高。
精益管理的全面实施使我们的工作场地地物明朗化,大大减少了寻找资料和物品的时间,工作效率有很大的提高。
把精益管理的理念带到自己的工作中,力求完美高质;及时对我们的文档资料的资源进行整理等习惯通过推行、实施精益管理,使我们的环境整洁、地物明朗、员工行为规范,大家认识到工作不仅要认真、细致、热情、负责,还要不断地学习、总结、改进,提高自己的工作质量,工作人员心情舒畅,士气必将得到提高。
同时,
精益管理的实施,可以减少人员、设备、场所、时间等等的浪费,从而降低工作运行和办公成本。
当然,做好一时并不困难,而长期坚持靠的则是我们的素养。
这是精益管理工作的目的,也是我们的工作目的。
今后,我们应该以精益管理工作为契机,抓住机遇、发扬“齐心共管、整洁高效”的精神,不断提升管理水平,使我们南岸质监局在广大人民心中树立环境整洁、举止严谨、办事高效、公平公正的美好形象,为我局的持续发展做出相应的贡献。
篇六
吾生也有涯,而知也无涯”。
去年,公司通过时代光华管理学院对举办了企业管理知识的培训,经过一年的学习,我收获颇多。
深刻领会到,作为一名合格的中层管理者,应该如何更好、更合理掌控整个部门的生产运作;并领悟到,应该以管理促创新,以创新促生产,以“精益生产”理念为部门又好又快地发展保驾护航。
下面就“精益生产”谈一谈我的一些感想。
1973年爆发了第二次世界大战之后最严重的世界性经济危机——第一次石油危机。
日本经济出现了零增长的局面,几乎所有的企业都被逼到了亏损的境地,惟有丰田汽车公司例外。
这说明了丰田公司有一种抗拒风险的强有力的方法,这就是丰田生产方式(精益生产)。
而精益生产主要是彻底杜绝企业内部各种浪费,以提高生产效率、提升产品的质量。
而丰田公司经过半个世纪的不断探索与实践,丰田生产方式不断充实、发展、完善,已经形成了一个将科学管理、技术创新、信息革命融为一体的完整管理体系。
而现在在市场经济的大环境下企业要有竞争力就必须在精益生产方面下大功夫。
对于精益生产我们只是迈出万里长征的第一步,所以摆在我们面前的将会是一段难及慢长的历程。
而我们要全面开展精益生产必须要从人员的意识着手宣传、培训等工作,而实行动中要从简单容易的做起。
精益生产有以下特点:
一、“均衡化”与“多样化”
多样化也就是多品种及少批量,但多品种少批量如果控制不好会对我们的库存尾数造成压力,也就是说资金的积压。
要解决这些问题需要做好均衡化的管理,在库存量及合格率上的有效控制是做好多样化的基础。
二、杜绝各种浪费以提高生产效率
操作的浪费在我们的工作中时刻存在,如可找出这些浪费及改善是关键,要找出我们身边的浪费只有全员参与才能做到更全面。
要真正能达到杜绝各种浪费还要做大量的工作,需要大量的人力才能做到,所以我们做好宣传工作,动员全体员工积极参与才能杜绝各种浪费,达到提高生产效率的目的。
三、少人化、自动化
“少人化”是从“省人化”过度得来的,这需要提高员工的操作技能才可实现。
而“自动化”除了设备自动化外,我觉得作为生产部门,人的“自动化”由其重要,人的“自动化”指我们每一个人都能自动去做事,自动去寻找问题并寻求解决措施,只有这样才能挖掘第一个人的潜力,使到在少人的情况下能完成预期的工作任务。
所以我们在人员的思想教育方面要多下功夫,使员工的意识上提高做到发处内心的自愿去做,只有这样才能达到“自动化”。
四、柔性生产
“柔性生产”实际就是我们常说的“一岗多能”,如果我们每一个员工能够掌握多个岗位的操作技能,那么在生产上人员的调动方面较为灵活,是少人化、自动化及杜绝浪费提高生产效率的基础。
要使每一个员工能掌握多个岗位的技能必须多给员工有培训及实践的机会,我们要多关心他们的学习及给予分配不同的工作,让他们在理论及实践中提高操作质能。
对部门发展的思考:
1、设立有关整顿浪费的制度,降低工人提出改进、创新的门槛。
工人只要提出合理、且对生产有益的改进就算一项成果,到年底的时候评比出优秀的成果,给予奖励和公布。
这样才能激发工人的创造热情,将员工的智慧充分加以利用,也就是先将第八大浪费减到最小。
2、生产计划要尽可能的细致和科学。
因为粗放的计划,肯定会造成库存和搬运的浪费,但是科学的计划还需要在下达计划的先期进行细致的工作,将各项零部件的生产节拍掌握清楚,然后再制订出科学的计划,避免不需要的零件堆满现场的弊端。
3、让现场管理真正地为生产服务。
现场管理应是生产管理的基石,而不应是障碍。
丰田公司的“5s管理”就是为整顿现场的浪费而服务的,只有建立起现场管理为生产服务的理念,才能将现场管理真正地做好。
4、工艺人员在编制工艺时,对加工余量的大小应科学、适当,避免不必要的加工和多余的加工,并且在审图时,对图中加严要求的地方应与设计及时沟通,不必要的加严应放松,以减少加工难度和加工时间。
5、对产品质量问题的处理不能仅停留在事后管理的层面上。
应制定改善问题的制度,为持续改善创造条件,创造出勇于和乐于面对问题的氛围,并提供对员工的方法培训,以加强对问题的追溯能力和解决问题的能力,从而真正做到全员抓质量的目的。
最后,我觉得,只要能够从一点一滴的小事改起,将精益的理念逐渐地渗透于日常的生产中,精益总会带来意想不到的收获。
我相信总有一天,当我们面临生产计划跟不上变化的时候,不是改变计划,而是学会控制变化。